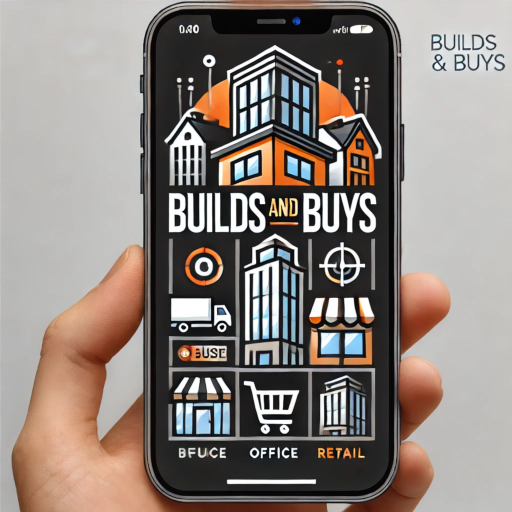
Check out our app!
Explore more features on mobile.
Insulation and Drywall Installation: Strategic Implementation Guide for Real Estate Investors
Insulation and drywall represent critical building envelope components that significantly impact energy efficiency, comfort, sound control, fire resistance, and overall property value. For real estate investors, these seemingly basic materials demand strategic consideration as they directly influence both construction costs and long-term property performance. According to the Department of Energy, proper insulation can reduce heating and cooling costs by 15-30%, while quality drywall installation affects everything from aesthetic appeal to resale value.
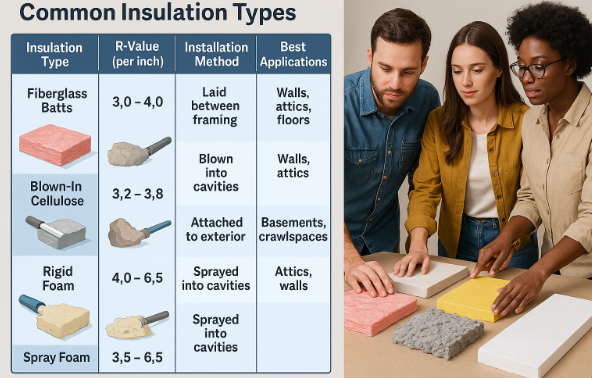
Strategic Planning for Insulation and Drywall
Effective insulation and drywall strategies begin with comprehensive planning that addresses both immediate construction needs and long-term property performance. The North American Insulation Manufacturers Association (NAIMA) reports that thoughtful insulation planning can reduce energy costs by up to 30% while enhancing occupant comfort and property value.
Key strategic considerations for real estate investors include:
- Climate zone requirements – Matching insulation R-values to regional climate conditions
- Building envelope design – Creating a continuous thermal and air barrier throughout the structure
- Moisture management strategy – Preventing condensation and water intrusion issues
- Sound attenuation needs – Addressing acoustic requirements between spaces
- Fire resistance planning – Meeting or exceeding code requirements for life safety
Building Science Fundamentals
Understanding building science principles enables better decision-making for insulation and drywall implementation. According to the Building Science Corporation, key concepts include:
- Heat flow mechanics – Conduction, convection, and radiation transfer mechanisms
- Air leakage impacts – Up to 40% of energy loss occurs through air infiltration
- Vapor diffusion concerns – Managing water vapor movement through building assemblies
- Thermal bridging – Heat transfer through framing members and penetrations
- Condensation prevention – Maintaining surface temperatures above dew point
The Department of Energy emphasizes that a whole-building approach to insulation and air sealing typically delivers 20-30% better performance than addressing individual components in isolation.
Pre-Installation Planning
Thorough preparation before insulation and drywall installation significantly impacts project efficiency and quality outcomes. The Gypsum Association recommends these key planning considerations:
- Mechanical, electrical, and plumbing coordination – Ensuring all systems are properly installed and inspected
- Framing inspection – Verifying proper spacing, blocking, and structural integrity
- Moisture content verification – Ensuring framing has appropriate moisture levels (typically below 19%)
- Environmental conditions – Maintaining proper temperature and humidity during installation
- Material acclimation – Allowing drywall to adjust to installation environment for 24-48 hours
Investment Perspective: Performance Longevity
The Building Performance Institute notes that properly designed and installed insulation and drywall systems maintain their performance for 40+ years in most applications. This longevity makes them particularly impactful for long-term investment properties, as their benefits compound over time through reduced energy costs, lower maintenance expenses, and enhanced property durability.
Insulation Types, Performance, and Selection Criteria
The insulation market offers diverse product options with varying performance characteristics, installation requirements, and cost considerations. According to the Environmental Protection Agency’s ENERGY STAR program, selecting the right insulation type for specific applications can impact energy performance by 10-30% beyond simply meeting minimum R-value requirements.
Insulation Type | R-Value per Inch | Typical Applications | Key Advantages | Limitations |
---|---|---|---|---|
Fiberglass Batts | 3.1 – 3.7 | Walls, floors, ceilings with standard framing | Cost-effective, widely available, non-combustible | Performance gaps around obstacles, susceptible to moisture |
Blown Fiberglass | 2.2 – 2.7 | Attics, hard-to-reach areas, retrofits | Fills irregular spaces, good sound absorption | Settling over time, lower R-value per inch |
Cellulose | 3.2 – 3.8 | Attics, wall cavities, retrofits | Recycled content, better air sealing, good sound control | Moisture sensitivity, settling potential, dust during installation |
Closed-Cell Spray Foam | 6.0 – 7.0 | Walls, ceilings, rooflines, rim joists | Air barrier, vapor barrier, structural enhancement | Higher cost, professional installation required |
Open-Cell Spray Foam | 3.5 – 3.7 | Interior walls, sound control applications | Air sealing, sound absorption, lower cost than closed-cell | Not a vapor barrier, absorbs moisture |
Rigid Foam Boards | 4.0 – 6.5 | Basement walls, continuous exterior insulation | High R-value per inch, moisture resistance | Requires meticulous sealing at joints, typically needs fire barrier |
Mineral Wool | 3.0 – 4.0 | Fire-resistant applications, sound control | Fire resistance, water repellent, excellent sound absorption | Higher cost than fiberglass, less widely available |
Source: Department of Energy, North American Insulation Manufacturers Association, and manufacturer data (2023)
R-Value Requirements by Climate Zone
The International Energy Conservation Code (IECC) establishes minimum R-value requirements that vary by climate zone:
- Attics/Ceilings – Range from R-30 in milder climates to R-60 in severe cold regions
- Walls – Range from R-13 in warm zones to R-21+5 (cavity plus continuous) in cold regions
- Floors – Range from R-13 in southern states to R-38 in northern regions
- Basements/Crawlspaces – Range from R-0 in warm zones to R-15 continuous or R-19 cavity in cold climates
- Slab Edges – Range from no requirement in warm zones to R-10 for 4 feet in cold regions
The Department of Energy recommends exceeding these minimum requirements by 25-30% for optimal performance in high-performance buildings and investment properties focused on energy efficiency.
Installation Methods and Quality Considerations
The effectiveness of insulation depends heavily on installation quality. The Building Performance Institute cites research showing that poor installation can reduce insulation performance by 25-40%. Key considerations include:
- Complete coverage – Ensuring all required areas are fully insulated without gaps or compression
- Void prevention – Properly fitting insulation around obstacles, wiring, and penetrations
- Air sealing integration – Addressing air leakage pathways before or in conjunction with insulation
- Moisture management – Including appropriate vapor control based on climate and assembly design
- Density verification – Ensuring proper installed density for loose-fill applications
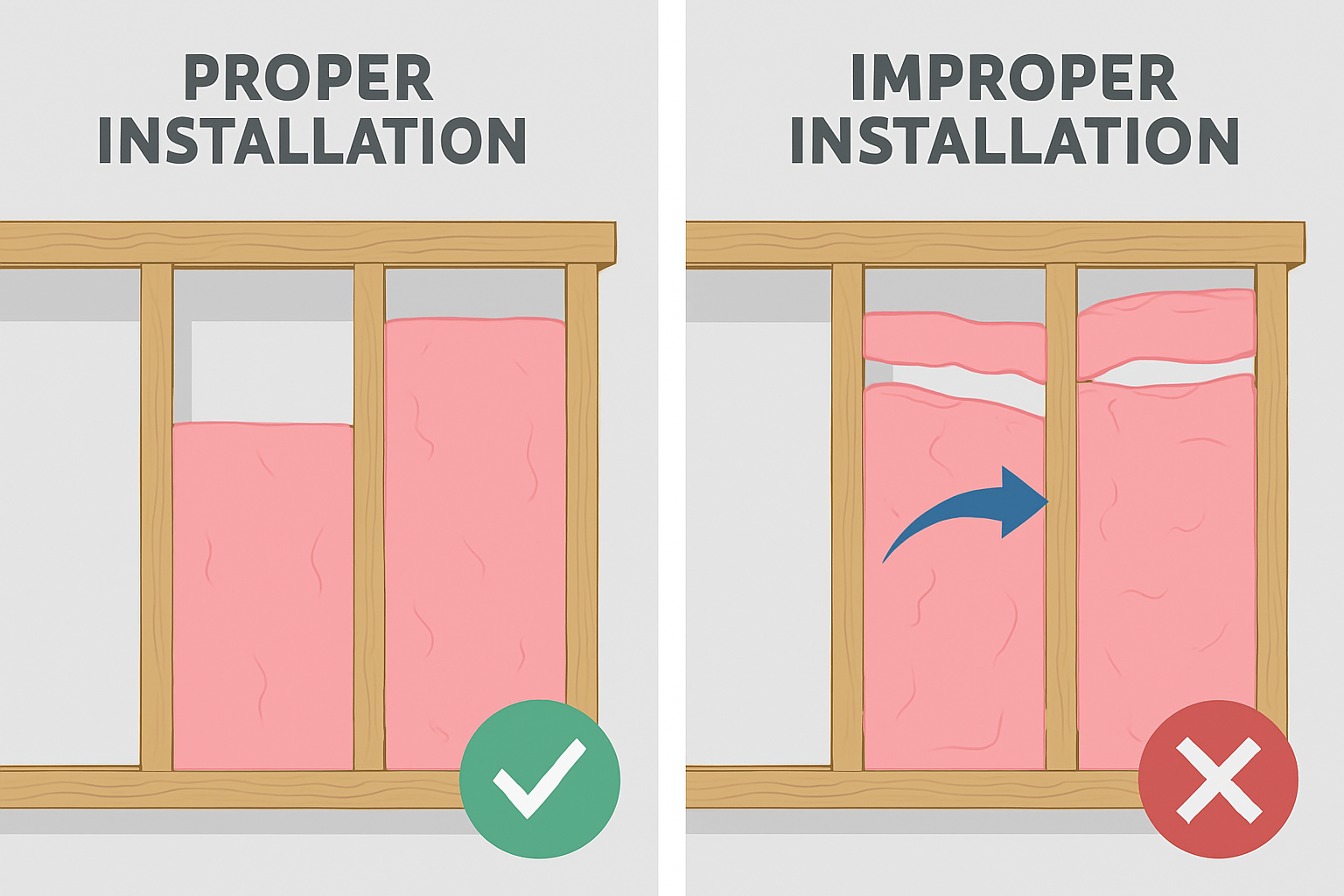
[Image: Side-by-side comparison of proper and improper insulation installation techniques]
Specialized Applications
Certain building areas require specialized insulation approaches for optimal performance:
- Rim/band joists – Critical areas for air leakage and thermal bridging requiring careful treatment
- Attic knee walls – Vertical walls in attic spaces requiring special attention to prevent thermal bypass
- Dropped ceilings – Areas below attics but lower than main ceiling plane needing special detailing
- Cantilevered floors – Projections beyond foundation walls requiring complete thermal enclosure
- Shower/tub exterior walls – Areas prone to condensation requiring careful insulation and air sealing
Drywall Materials and Installation Considerations
Drywall (also called gypsum board or wallboard) serves multiple functions in buildings, including fire resistance, sound control, and creating a finished surface for paint or wallcoverings. According to the Gypsum Association, proper drywall selection and installation significantly impact both construction quality and long-term building performance.
Drywall Types and Applications
The gypsum board market offers specialized products for different applications and performance requirements:
Drywall Type | Key Characteristics | Best Applications | Cost Premium* |
---|---|---|---|
Standard (Regular) | Basic 1/2″ thickness, general purpose | Walls in dry areas, general applications | Base cost |
Moisture-Resistant (Green Board) | Water-resistant core and facing | Bathrooms, laundry rooms, kitchens (non-wet areas) | +15-30% |
Mold-Resistant | Treated paper or paperless facing | Basements, humid environments, moisture-prone areas | +30-50% |
Fire-Resistant (Type X) | Glass fibers and additives for enhanced fire resistance | Garages, furnace rooms, code-required fire separations | +20-35% |
Ceiling Board | Lighter weight, sag-resistant formulation | Horizontal ceiling applications | +10-20% |
Soundproof/Acoustic | Laminated or engineered for sound attenuation | Bedrooms, home offices, multi-family separations | +70-100% |
Abuse-Resistant | Reinforced to resist surface damage | High-traffic areas, rental properties, commercial spaces | +40-75% |
Cement Board | Cement-based, completely water-resistant | Tile substrate in showers, tub surrounds, exteriors | +100-150% |
*Cost premium compared to standard drywall; varies by market. Source: Gypsum Association and industry pricing data (2023)
Drywall Thickness Considerations
Selecting the appropriate drywall thickness affects performance, cost, and installation requirements:
- 1/4-inch – Primarily used for curved surfaces or overlaying existing walls
- 3/8-inch – Occasional use for repairs or layering, rarely used as primary wall surface
- 1/2-inch – Standard for most residential wall applications, common in new construction
- 5/8-inch – Used for fire-rated assemblies, ceiling applications, and providing greater sound control
- Multiple layers – Used in high-performance sound control assemblies or to achieve specific fire ratings
Installation Methods and Quality Factors
According to the Association of the Wall and Ceiling Industry, installation quality significantly impacts both aesthetic outcomes and functional performance. Key installation considerations include:
- Panel orientation – Horizontal vs. vertical installation depending on wall height and application
- Fastener selection – Screws vs. nails, length, and spacing requirements
- Joint treatment systems – Paper tape vs. mesh tape, compound types, and application methods
- Corner reinforcement – Paper-faced, metal, or composite corner bead options
- Control joint placement – Accommodating structural movement in larger wall and ceiling areas
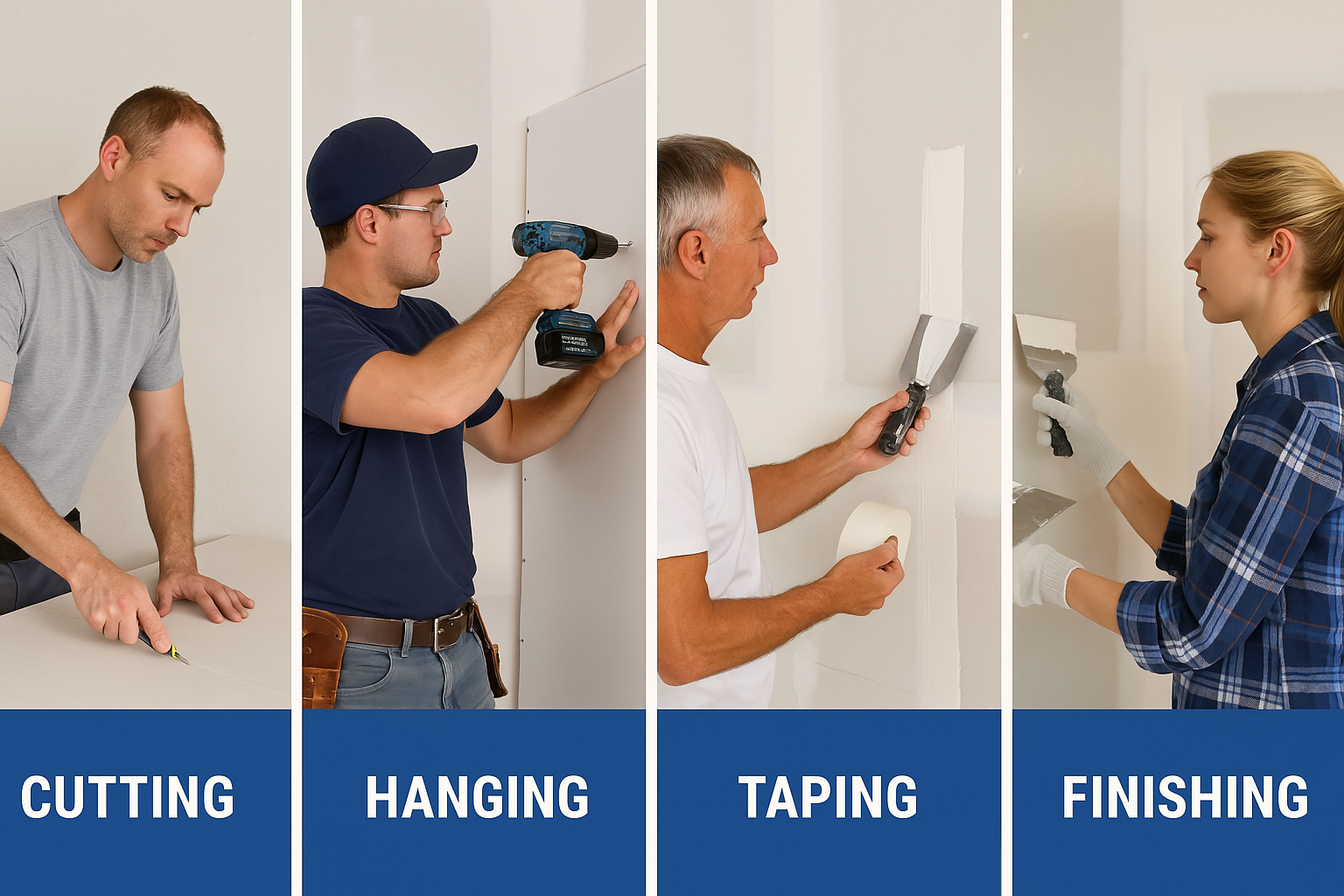
[Image: Step-by-step visualization of professional drywall installation techniques]
Specialized Installation Considerations
Certain applications require specialized drywall installation approaches:
- Fire-rated assemblies – Specific board types, fastening patterns, and joint treatment requirements
- Sound-rated partitions – Staggered seams, acoustical sealants, and specific mounting methods
- High-moisture environments – Proper board selection, moisture-resistant fasteners, and specialized finishes
- Curved surfaces – Pre-wetting techniques, specialized thin panels, or multiple thin layers
- Ceiling applications – Additional support requirements and sag-resistant board selection
Finishing Levels and Appearance Considerations
The Gypsum Association defines industry-standard finishing levels that specify the degree of finish quality:
- Level 0 – Temporary construction or substrate for other materials; no taping or finishing
- Level 1 – Fire-taped only (joints with tape embedded in joint compound); typically for plenum areas
- Level 2 – Taped and one coat of compound over fasteners and accessories; typically for garages, storage areas
- Level 3 – Taped with two coats of compound; suitable for surfaces receiving heavy textured finishes
- Level 4 – Standard finish with three coats of compound; suitable for flat paints and light textures
- Level 5 – Highest quality finish with skim coat over entire surface; required for glossy paints or critical lighting
Research by the Drywall Finishing Council indicates that finish level selection significantly impacts final appearance, with Level 5 finishes reducing visible surface defects by approximately 70-80% compared to Level 4 when using semi-gloss or glossy paints.
Code Requirements and Performance Standards
Insulation and drywall installations are subject to various building codes and industry standards that establish minimum requirements for performance, safety, and durability. Understanding these requirements is essential for compliance and avoiding costly remediation.
Energy Code Requirements
The International Energy Conservation Code (IECC) and ASHRAE Standard 90.1 establish minimum requirements for building thermal performance:
- Prescriptive R-value path – Specifies minimum insulation levels for different building components
- U-factor alternative – Performance-based approach allowing trade-offs between components
- Total UA alternative – Calculation method allowing area-weighted averaging across envelope
- Performance path – Energy modeling approach demonstrating equivalent or better performance
- Air leakage requirements – Maximum allowed air changes per hour through building envelope
Fire Resistance Requirements
The International Building Code (IBC) and International Residential Code (IRC) establish fire resistance requirements that affect both insulation and drywall selections:
- Flame spread and smoke development – Maximum ratings for materials based on occupancy type
- Fire separation assemblies – Rated wall and ceiling designs for separating occupancies or spaces
- Garage separation requirements – Typically requiring 5/8″ Type X gypsum board or equivalent
- Multi-family separation walls – One- and two-hour rated assemblies with specific component requirements
- Thermal barrier requirements – Covering for foam plastic insulation materials (typically 1/2″ gypsum board)
According to the Gypsum Association, properly installed 5/8″ Type X gypsum board provides approximately 60 minutes of fire resistance when applied to each side of a wood or metal stud wall.
Sound Transmission Requirements
Various codes establish minimum requirements for sound control, particularly in multi-family construction:
- Sound Transmission Class (STC) – Measures airborne sound transmission through assemblies
- IRC requires minimum STC 45 between dwelling units
- FHA minimum STC 50 for walls and floors between units
- High-performance designs often target STC 55-60+
- Impact Insulation Class (IIC) – Measures impact sound transmission through floor/ceiling assemblies
- IRC requires minimum IIC 45 between dwelling units
- FHA minimum IIC 50 for floor/ceiling assemblies
- High-performance designs often target IIC 55-60+
Moisture Management and Vapor Control
Building codes include specific requirements for vapor retarders and moisture control that vary by climate zone:
- Vapor retarder classifications – Class I (≤0.1 perm), Class II (0.1-1.0 perm), Class III (1.0-10 perm)
- Climate-specific requirements – Different vapor control strategies for different climate zones
- Wet area specifications – Special requirements for bathrooms, laundry rooms, and other wet areas
- Water-resistant backing materials – Requirements for tile and other wet-area wall coverings
- Exterior insulation considerations – Impact on wall drying potential and vapor drive direction
Critical Compliance Warning
Building Science Corporation research indicates that moisture management failures account for approximately 80% of building envelope failures and associated legal claims. Improper vapor barrier installation or inappropriate selection for the climate zone can trap moisture within assemblies, leading to mold, rot, and premature building failure.
Key risk mitigation strategy: Always verify climate-appropriate vapor control strategies with a qualified building science professional, particularly when implementing high-performance insulation strategies or working in high-humidity environments.
Green Building Standards
Various voluntary green building programs establish enhanced requirements for insulation and drywall:
- ENERGY STAR – Enhanced insulation levels, comprehensive air sealing, and thermal bridge reduction
- LEED – Points for enhanced insulation, recycled content, low-emission materials, and regional sourcing
- National Green Building Standard – Tiered insulation requirements and material resource efficiency
- Passive House – Extremely high insulation levels, thermal bridge-free design, and airtightness
- Zero Energy Ready Home – Climate-specific high-performance envelope requirements
Cost Analysis and ROI Calculations
Strategic insulation and drywall investments require careful financial analysis that considers both initial installation costs and long-term performance benefits. According to the National Association of Home Builders, insulation and drywall typically represent 3-5% of total construction costs but significantly impact ongoing operating expenses and property value.
Component | Code Minimum Cost | Enhanced Performance Cost | Premium Performance Cost |
---|---|---|---|
Wall Insulation (2,000 sq ft home) | $1,800-$2,500 (R-13 fiberglass batts) |
$3,000-$4,500 (R-19 with air sealing) |
$7,000-$12,000 (Spray foam system) |
Attic Insulation (1,500 sq ft area) | $1,500-$2,200 (R-38 blown fiberglass) |
$2,200-$3,000 (R-49 blown fiberglass) |
$3,000-$5,000 (R-60 with air sealing) |
Basement/Crawlspace Insulation | $1,200-$2,500 (Basic perimeter) |
$2,500-$4,000 (Full wall coverage) |
$4,000-$7,000 (Spray foam system) |
Drywall Installation (2,000 sq ft home) | $7,000-$10,000 (Standard 1/2″ board, Level 4 finish) |
$10,000-$13,000 (Mix of specialty boards, Level 4) |
$13,000-$18,000 (Premium boards, Level 5 finish) |
Air Sealing Package | $500-$1,000 (Basic sealing at major penetrations) |
$1,200-$2,500 (Comprehensive air sealing) |
$2,500-$4,000 (Advanced system with testing) |
Sound Control Upgrades | $500-$1,000 (Basic bathroom insulation) |
$2,000-$3,500 (Selected room treatments) |
$5,000-$9,000 (Whole-house acoustic package) |
Note: Costs represent national averages and may vary by region (±20%). Source: HomeAdvisor, RSMeans, National Association of Home Builders (2023 data)
Energy Savings Return on Investment
The Department of Energy provides data demonstrating the financial impact of insulation and air sealing improvements:
- Attic insulation upgrade – Upgrading from R-30 to R-60 in cold climates typically yields 5-8% heating cost savings with payback periods of 5-7 years
- Wall insulation improvement – Enhancing wall insulation beyond code minimum typically yields 10-15% energy savings with payback periods of 7-10 years
- Comprehensive air sealing – Professional air sealing can reduce heating/cooling costs by 15-20% with payback periods of 3-5 years
- Basement insulation – Properly insulating basement walls typically yields 10-15% energy savings with payback periods of 5-8 years
- Crawlspace encapsulation – Complete crawlspace treatments yield 15-20% energy savings plus moisture control benefits with payback periods of 5-10 years
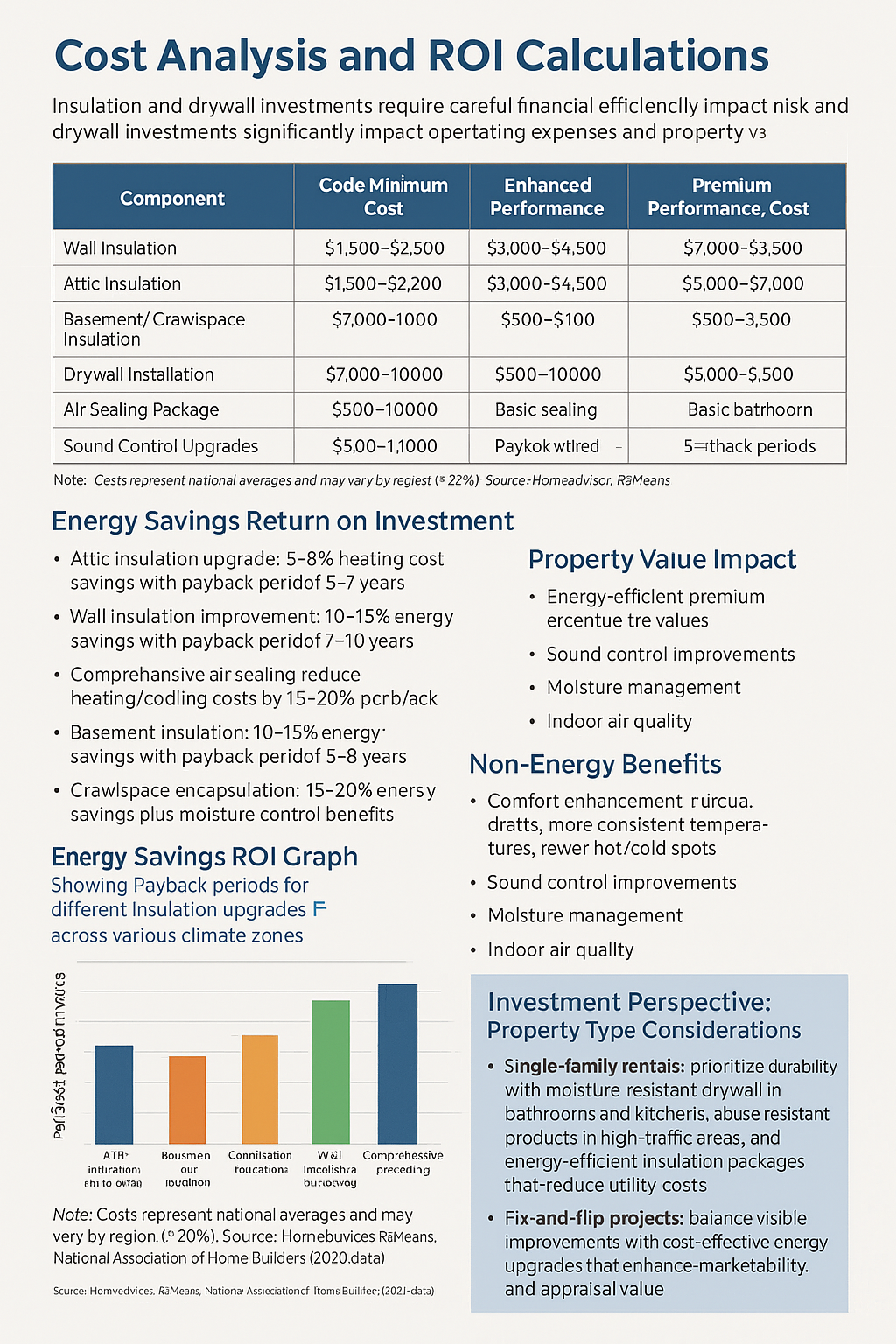
[Image: Comparative ROI analysis for insulation upgrades across different climate zones]
Property Value Impact
Research from the National Association of Realtors and Appraisal Institute indicates that energy-efficient improvements including insulation and air sealing can enhance property values:
- Energy efficiency premium – Properties with documented high performance typically command 2-6% higher values
- Certification value – ENERGY STAR, LEED, or other certified homes sell for 3-8% more than comparable conventional homes
- Marketing advantage – Energy-efficient homes typically sell 20-30% faster than comparable conventional homes
- Appraisal recognition – Increasing appraiser recognition of energy features through Appraisal Institute’s green addendum
- Mortgage benefits – Energy-efficient mortgages and green lending programs offering enhanced terms for efficient properties
Non-Energy Benefits
Properly implemented insulation and drywall systems provide significant non-energy benefits that impact property value and marketability:
- Comfort enhancement – Reduced drafts, more consistent temperatures, and fewer hot/cold spots
- Sound control improvements – Enhanced privacy, reduced exterior noise intrusion, and better room-to-room sound isolation
- Moisture management – Reduced condensation risk, better humidity control, and lower mold potential
- Indoor air quality – Better filtration opportunities and reduced infiltration of outdoor pollutants
- Durability improvements – Extended building component life through better moisture and temperature control
Investment Perspective: Property Type Considerations
Different property types benefit from specific insulation and drywall investment strategies:
- Single-family rentals: Prioritize durability with moisture-resistant drywall in bathrooms and kitchens, abuse-resistant products in high-traffic areas, and energy-efficient insulation packages that reduce utility costs
- Multi-family properties: Focus on sound control between units, fire separation requirements, and energy efficiency measures that can be marketed as tenant benefits
- Fix-and-flip projects: Balance visible improvements with cost-effective energy upgrades that enhance marketability and appraisal value
- Long-term investment properties: Implement comprehensive insulation and air sealing strategies that minimize maintenance and maximize energy performance over time
- Luxury properties: Incorporate premium acoustical treatments, Level 5 drywall finishes, and high-performance insulation packages that support comfort marketing and property differentiation
Builds and Buys Approach: Implementation Framework
At Builds and Buys, we’ve developed a systematic approach to insulation and drywall implementation that maximizes investment returns while ensuring proper system performance:
Step-by-Step Builds: Implementation Strategy
Our comprehensive approach to new construction and renovation projects:
- Climate-specific design – Tailoring insulation and moisture control strategies to local conditions
- Thermal boundary mapping – Clearly defining and maintaining continuous thermal and air barriers
- Pre-insulation inspection protocol – Verifying framing, mechanical systems, and moisture conditions
- Installation quality management – Implementing verification steps throughout the process
- Performance testing integration – Using blower door and infrared imaging to verify outcomes
Step-by-Step Buys: Evaluation Framework
For investors evaluating existing properties, our inspection framework provides critical insights:
- Insulation verification methods – Non-destructive techniques to assess existing insulation
- Thermal bypass identification – Locating critical performance gaps in the thermal envelope
- Moisture problem detection – Identifying existing or potential moisture management issues
- Upgrade opportunity analysis – Evaluating cost-effective improvement options
- Drywall condition assessment – Evaluating surface quality, damage, and repair needs
Step-by-Step Invest: Financial Optimization
Our investment strategies help allocate resources for maximum financial performance:
- Energy modeling analysis – Quantifying expected returns from insulation investments
- Performance tier optimization – Identifying the optimal insulation levels for specific properties
- Incentive capture strategy – Maximizing available rebates, tax credits, and utility programs
- Material selection matrix – Balancing cost, performance, and property-specific requirements
- Long-term value calculation – Projecting lifetime returns including energy, maintenance, and resale
Quality Assurance and Inspection Protocols
Implementing systematic quality assurance measures ensures that insulation and drywall installations deliver their intended performance benefits. The Building Performance Institute and Residential Energy Services Network recommend comprehensive inspection protocols at critical stages.
Pre-Insulation Inspection Checklist
- ☐ Framing Verification
- ☐ Proper stud spacing and alignment for insulation installation
- ☐ Required blocking and backing for drywall installed
- ☐ Window and door openings properly framed and flashed
- ☐ Framing moisture content verified (should be below 19%)
- ☐ Required fire blocking installed per code
- ☐ Mechanical Systems Readiness
- ☐ All plumbing rough-in complete and tested
- ☐ Electrical wiring properly installed and inspected
- ☐ HVAC ducts and equipment properly installed
- ☐ All mechanical penetrations through building envelope addressed
- ☐ Required clearances around mechanical equipment maintained
- ☐ Air Sealing Preparation
- ☐ Top and bottom plates sealed to adjacent materials
- ☐ Penetrations through plates and framing sealed
- ☐ Window and door rough openings sealed
- ☐ Electrical boxes and wire penetrations sealed
- ☐ Plumbing and mechanical penetrations sealed
Insulation Installation Inspection
- ☐ Material Verification
- ☐ Correct insulation type and R-value for each application
- ☐ Proper fasteners and supports for the insulation type
- ☐ Vapor retarder type appropriate for climate zone and location
- ☐ Materials protected from moisture and damage
- ☐ Manufacturer labels visible for inspection
- ☐ Installation Quality
- ☐ Insulation completely fills cavities without gaps or compression
- ☐ Insulation split around wiring, plumbing, and other obstacles
- ☐ Proper support to prevent sagging over time
- ☐ Blown insulation installed to proper depth and density
- ☐ Attic rulers installed to verify depth in blown applications
- ☐ Critical Areas Verification
- ☐ Rim/band joists properly insulated and air sealed
- ☐ Attic hatches and access points insulated to same R-value as surrounding area
- ☐ Knee walls properly insulated with rigid backing
- ☐ Attic baffles installed to maintain ventilation paths
- ☐ Wall insulation properly trimmed at electrical boxes
Pre-Drywall Inspection
- ☐ Surface Preparation
- ☐ Framing square and plumb within tolerances
- ☐ All insulation complete and passes inspection
- ☐ Required blocking installed at panel edges
- ☐ All mechanical rough-ins complete and inspected
- ☐ Environmental conditions appropriate for installation
- ☐ Material Verification
- ☐ Correct drywall type for each application (moisture-resistant, fire-rated, etc.)
- ☐ Proper thickness for the application
- ☐ Materials acclimated to installation environment
- ☐ Appropriate fasteners for the application
- ☐ Joint compound and tape compatible with board type
Drywall Installation Inspection
- ☐ Mounting Technique
- ☐ Panels oriented correctly (horizontal vs. vertical per plan)
- ☐ Joints staggered appropriately
- ☐ Proper spacing at floor (1/4″ – 3/8″ gap)
- ☐ Proper spacing at panel joints (1/8″ gap)
- ☐ Fasteners properly spaced and set
- ☐ Special Conditions
- ☐ Corner bead properly installed at outside corners
- ☐ Control joints installed where required
- ☐ Fire-rated assemblies installed per design requirements
- ☐ Proper treatment around doors and windows
- ☐ Access panels installed where required
- ☐ Finishing Quality
- ☐ Appropriate finish level achieved per specifications
- ☐ Joint tape properly embedded without wrinkles
- ☐ Fastener dimples properly covered
- ☐ Corner treatments square and straight
- ☐ Surface ready for specified paint finish
Performance Verification
- ☐ Blower door testing to verify building envelope tightness
- ☐ Infrared thermal imaging to verify insulation coverage
- ☐ Smoke testing to identify air leakage pathways
- ☐ Sound transmission testing for acoustically rated assemblies
- ☐ Moisture meter verification of drywall and framing moisture content
- ☐ Visual inspection under critical lighting conditions
- ☐ Documentation of all inspection results and verification tests
Professional vs. DIY Considerations
While some insulation and drywall tasks can be suitable for DIY projects, professional installation often delivers superior results for investment properties:
- Insulation installation – Professional installation typically achieves 15-25% better thermal performance due to proper filling techniques and attention to detail
- Air sealing expertise – Professionals identify and address critical air leakage pathways that DIYers often miss
- Drywall hanging efficiency – Professional crews can typically install drywall 3-4 times faster than DIYers with better results
- Finishing quality – Professional drywall finishing creates surfaces that are noticeably superior under both normal and critical lighting
- Warranty protection – Professional installation typically includes workmanship guarantees and better material warranty coverage
Maintenance and Long-Term Care
Proper maintenance ensures that insulation and drywall continue to perform as intended throughout the building’s life:
- Periodic inspection – Check for signs of moisture intrusion, settling insulation, or drywall damage
- Attic insulation monitoring – Verify depth and coverage annually, especially after work in the attic
- Water leak response – Address any water damage to drywall promptly to prevent mold and deterioration
- Penetration management – Properly seal any new penetrations through insulated assemblies
- Repair techniques – Use appropriate methods for drywall repairs to maintain appearance and performance
Discover more essential real estate investment strategies with our comprehensive guides on Step-by-Step Builds, Step-by-Step Buys, and Step-by-Step Invest.
Real Estate News And Knowledge
Stay informed with the latest trends, insights, and updates in the real estate world.
Your Tools
Access your tools to manage tasks, update your profile, and track your progress.
Collaboration Feed
Engage with others, share ideas, and find inspiration in the Collaboration Feed.