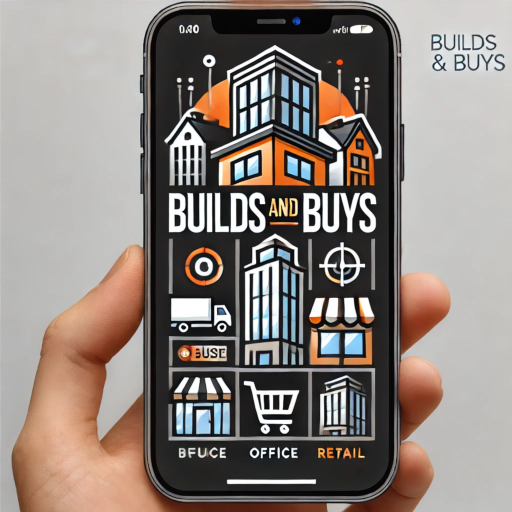
Check out our app!
Explore more features on mobile.
Exterior Finishes: Strategic Implementation Guide for Real Estate Investors
Exterior finishes form the critical protective envelope of a property while simultaneously creating the crucial first impression that influences market value and curb appeal. For real estate investors, these elements represent both a significant capital expenditure and a strategic opportunity to enhance property performance. According to the National Association of Realtors, exterior appearance significantly impacts property valuation, with enhanced curb appeal potentially increasing perceived value by 5-12%.
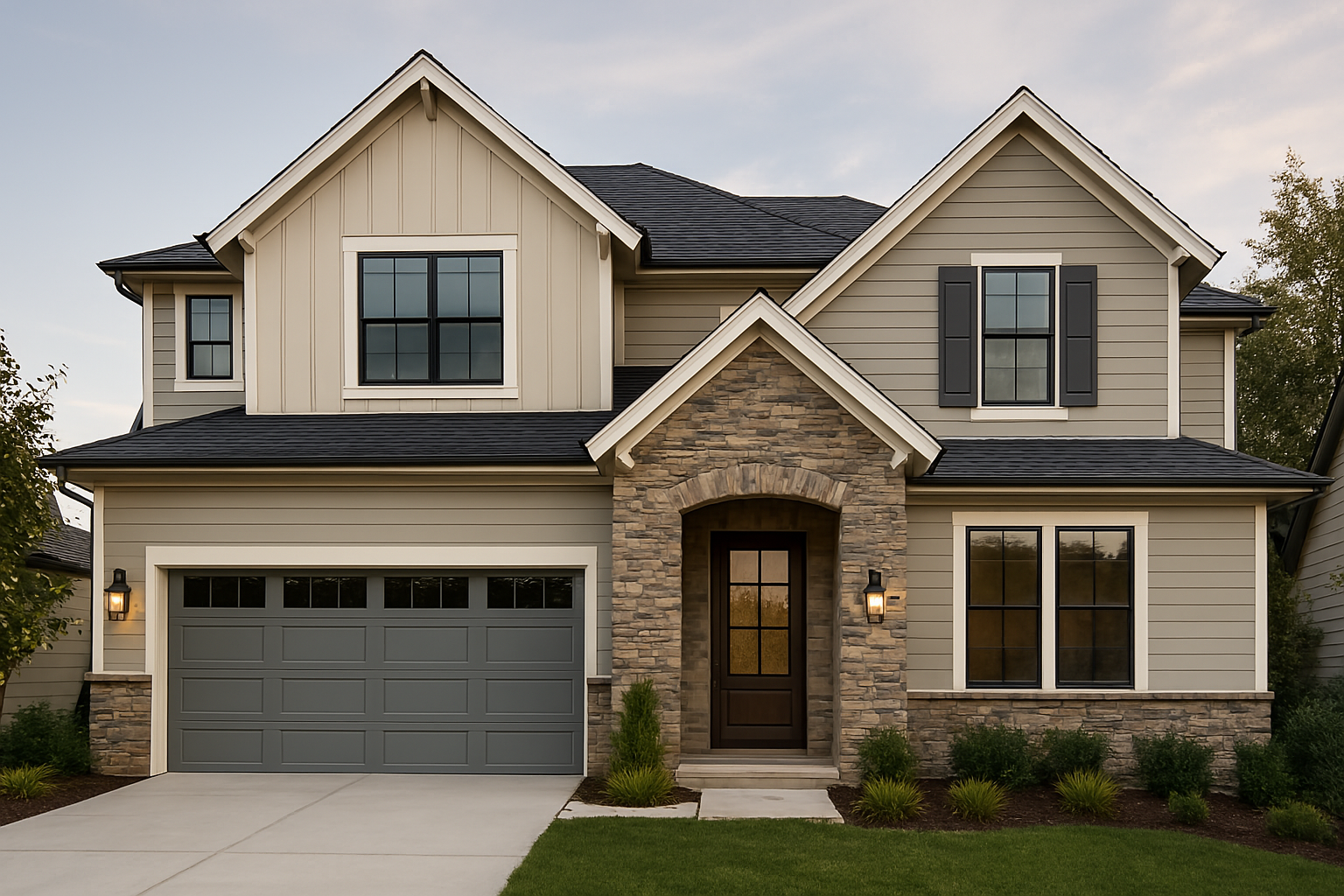
[Image: Visual comparison of exterior finish options with performance characteristics and aesthetic impacts]
Strategic Planning for Exterior Finishes
Effective exterior finish planning requires balancing multiple factors including durability, climate appropriateness, maintenance requirements, and market expectations. According to the Building Science Corporation, a comprehensive exterior strategy should address both protective function and aesthetic considerations.
Key strategic considerations for real estate investors include:
- Climate resilience – Selecting materials appropriate for local weather conditions and natural hazards
- Maintenance planning – Balancing upfront costs with long-term care requirements
- Neighborhood context – Aligning with local architectural standards while providing appropriate differentiation
- Energy efficiency impact – Considering how exterior selections affect thermal performance
- Investment timeline alignment – Matching material longevity with intended holding period
Climate and Regional Considerations
The International Association of Certified Home Inspectors emphasizes that local climate conditions significantly impact exterior material performance:
- Coastal environments – Salt exposure necessitates corrosion-resistant materials and enhanced moisture protection
- High precipitation regions – Require superior moisture management and rot-resistant materials
- Extreme temperature zones – Need materials with appropriate thermal expansion properties
- High UV exposure areas – Demand fade-resistant finishes and UV-stable materials
- Wind-prone locations – Require enhanced attachment methods and impact-resistant materials
- Wildfire risk zones – Need fire-resistant exterior materials and specific construction details
Research from the Insurance Institute for Business and Home Safety demonstrates that climate-appropriate exterior selections can reduce weather-related damage by 40-70% and extend material service life by 25-50%.
Budgeting and Value Optimization
Strategic budget allocation for exterior finishes should consider both initial costs and long-term performance:
- Lifecycle cost analysis – Evaluating total ownership costs including installation, maintenance, and replacement
- Visual impact prioritization – Allocating higher budgets to highly visible elements with maximum curb appeal impact
- Performance tier alignment – Matching material quality to property positioning and target market
- Protection hierarchy – Investing first in elements that prevent water intrusion and structural damage
- Enhancement sequencing – Planning the correct order of exterior improvements for maximum value
Investment Perspective: The 50-30-20 Principle
Remodeling Magazine’s Cost vs. Value report suggests the following budget allocation approach for optimal returns:
- 50% of budget – Directed toward primary protective systems (roofing, siding, windows) that form the weather-resistant barrier
- 30% of budget – Allocated to secondary elements that enhance function and appearance (trim, doors, outdoor living spaces)
- 20% of budget – Reserved for accent elements that create distinctive character (architectural details, specialty lighting, landscape integration)
This balanced approach ensures adequate investment in critical protective functions while allowing for strategic enhancements that maximize curb appeal and market differentiation.
Energy Efficiency Considerations
The Department of Energy notes that exterior finish selections significantly impact energy performance:
- Thermal bridging management – Reducing heat transfer through framing and structural elements
- Insulation integration – Coordinating exterior finishes with insulation strategies
- Air barrier continuity – Ensuring proper sealing and barrier integration with finish systems
- Solar reflectance impact – Selecting appropriate colors and materials for climate optimization
- Window performance factors – Balancing glazing properties with aesthetic considerations
Energy-efficient exterior strategies can reduce heating and cooling costs by 20-30% while potentially qualifying for tax incentives, rebates, and preferred financing options.
Siding and Cladding Options
Siding and cladding comprise the largest visible exterior surface and significantly impact both property protection and aesthetic character. According to the Vinyl Siding Institute and other industry associations, material selection should balance appearance, durability, maintenance requirements, and climate appropriateness.
Siding Type | Cost Range (Installed) | Expected Lifespan | Maintenance Requirements | Best Applications |
---|---|---|---|---|
Vinyl Siding | $4-$8 per sq ft | 20-40 years | Low (occasional cleaning) | Rental properties, budget-conscious renovations, starter homes |
Fiber Cement | $6-$12 per sq ft | 50+ years | Moderate (repainting every 7-15 years) | Long-term investments, mid to upper-tier properties, diverse climates |
Wood Siding | $8-$14 per sq ft | 20-40 years | High (regular staining/painting, inspections) | Historic properties, premium aesthetics, appropriate climates |
Engineered Wood | $5-$10 per sq ft | 20-30 years | Moderate (painting every 5-10 years) | Mid-range properties, wood look with reduced maintenance |
Metal/Steel | $5-$12 per sq ft | 40-60 years | Low (occasional cleaning, inspect fasteners) | Contemporary designs, severe weather regions, fire-prone areas |
Stone Veneer | $15-$50 per sq ft | 50+ years | Low (occasional cleaning, inspect mortar) | Luxury properties, accent areas, high-value markets |
Stucco | $7-$12 per sq ft | 40-50 years | Moderate (inspect for cracks, occasional cleaning) | Southwestern/Mediterranean styles, dry climates |
Composite/Synthetic | $7-$15 per sq ft | 25-50 years | Low (occasional cleaning) | Premium appearance with reduced maintenance needs |
Source: RSMeans, Home Innovation Research Labs, manufacturer data (2023)
Installation Best Practices
The Building Science Corporation emphasizes that installation quality significantly impacts siding performance regardless of material selection:
- Weather-resistant barrier integration – Proper housewrap or building paper installation and flashing details
- Moisture management systems – Rainscreen designs with drainage planes and ventilation
- Appropriate fastening methods – Material-specific attachment systems that accommodate movement
- Expansion allowances – Proper spacing and installation techniques for material movement
- Trim and transition details – Weatherproof interfaces between siding and other elements
- Penetration management – Proper flashing and sealing around fixtures, vents, and utilities
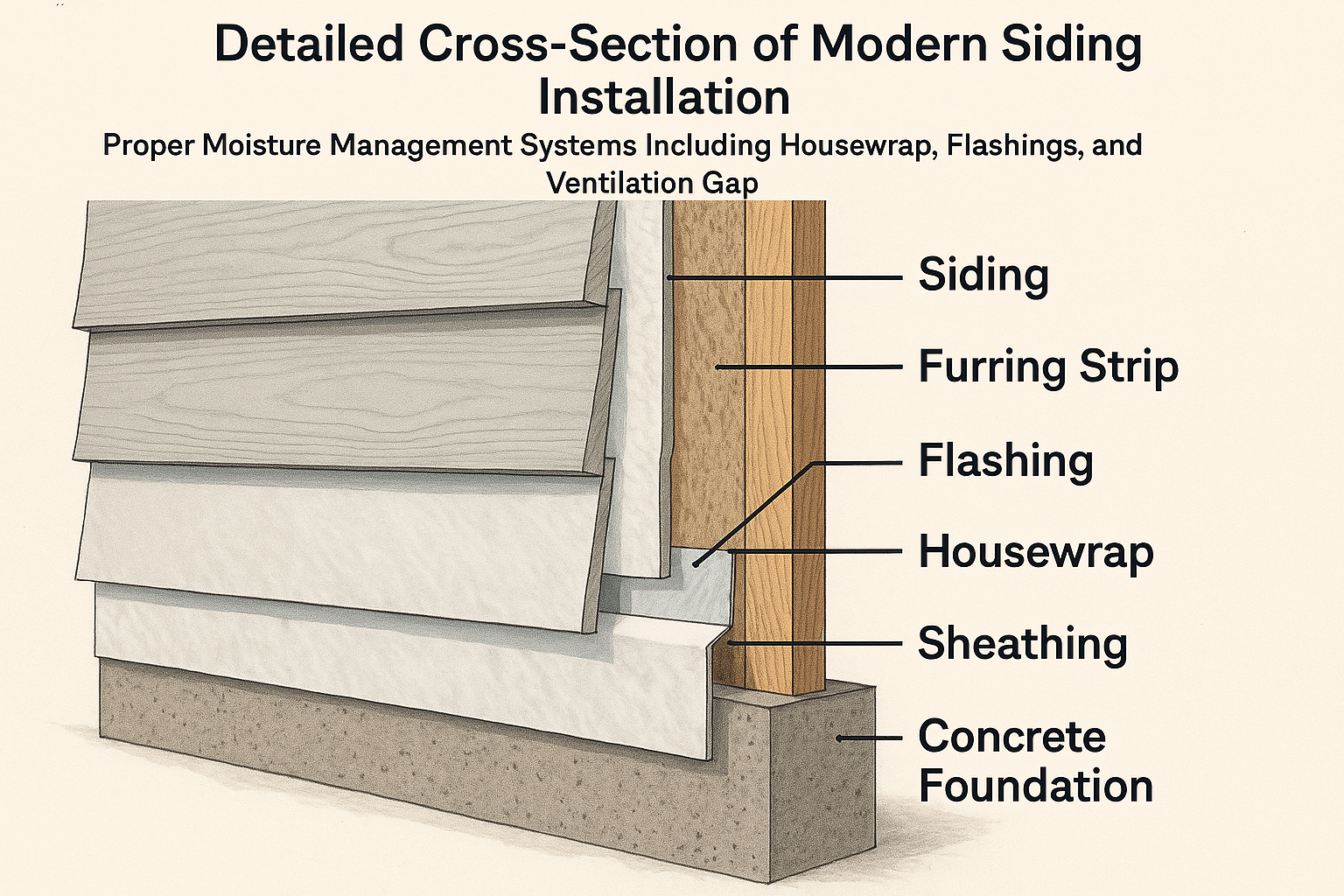
[Image: Cross-sectional diagram of proper siding installation with moisture management details]
Style and Aesthetic Considerations
The American Institute of Architects notes several factors that influence siding selection beyond purely functional considerations:
- Architectural compatibility – Aligning materials with property style and era
- Texture variations – Smooth, wood-grain, or textured finishes for visual interest
- Profile options – Lap, shake, board-and-batten, and panel designs for different looks
- Color considerations – Factory-finished vs. field-applied color options
- Mixed material strategies – Combining different siding types for visual interest and cost management
Market research from the National Association of Home Builders indicates that thoughtful siding selection and installation can increase property valuations by 5-10% while reducing time-on-market by 20-30% compared to properties with outdated or deteriorated exteriors.
Return on Investment Factors
Remodeling Magazine’s Cost vs. Value Report provides ROI data on various siding projects:
- Vinyl siding replacement – National average ROI of 68-70% with significant regional variations
- Fiber cement siding – National average ROI of 69-75%, higher in upscale neighborhoods
- Manufactured stone veneer – National average ROI of 91-95% when used as accent on front façade
- Wood siding – National average ROI of 63-69%, higher in historic districts and premium markets
- Insulated siding systems – ROI enhanced by energy efficiency benefits and potential utility incentives
Roofing Materials and Systems
Roofing represents both a critical protective system and a significant visual element that impacts property value. According to the National Roofing Contractors Association, roofing material selection should balance durability, performance, and aesthetic considerations.
Roofing Material | Cost Range (Installed) | Expected Lifespan | Key Advantages | Limitations |
---|---|---|---|---|
Asphalt Shingles (3-Tab) | $3.50-$5.50 per sq ft | 15-20 years | Cost-effective, wide availability, easy installation | Shorter lifespan, limited wind resistance, basic appearance |
Architectural Shingles | $4.50-$7.00 per sq ft | 25-30 years | Dimensional appearance, better wind resistance, moderate cost | Still vulnerable to extreme weather, moderate lifespan |
Metal Roofing | $7.00-$14.00 per sq ft | 40-70 years | Exceptional durability, fire resistance, energy efficiency | Higher initial cost, potential noise concerns, specialized installation |
Clay/Concrete Tile | $10.00-$18.00 per sq ft | 50+ years | Distinctive appearance, excellent durability, fire resistance | Heavy weight requires adequate structural support, higher cost |
Slate | $15.00-$30.00 per sq ft | 75-100+ years | Premium appearance, longest lifespan, excellent durability | Very heavy, highest cost, requires specialized installation |
Wood Shakes/Shingles | $6.50-$14.00 per sq ft | 20-40 years | Natural appearance, good insulation properties | Fire concerns, higher maintenance, not allowed in some areas |
Synthetic Roofing | $7.00-$15.00 per sq ft | 30-50 years | Mimics premium materials at lower weight/cost, good durability | Relatively new with limited long-term performance data |
Source: Roofing Contractors Association, RSMeans data, manufacturer specifications (2023)
Roofing System Components
The Asphalt Roofing Manufacturers Association emphasizes that a complete roofing system involves multiple components beyond visible materials:
- Underlayment selection – Traditional felt vs. synthetic underlayment characteristics and benefits
- Ice and water shield application – Critical areas requiring enhanced protection
- Ventilation integration – Balanced intake and exhaust systems for attic ventilation
- Flashing details – Proper materials and techniques for roof penetrations and transitions
- Ridge and hip treatments – Specialized materials for peak protection and appearance
- Gutter system coordination – Appropriate sizing and integration with roofing components
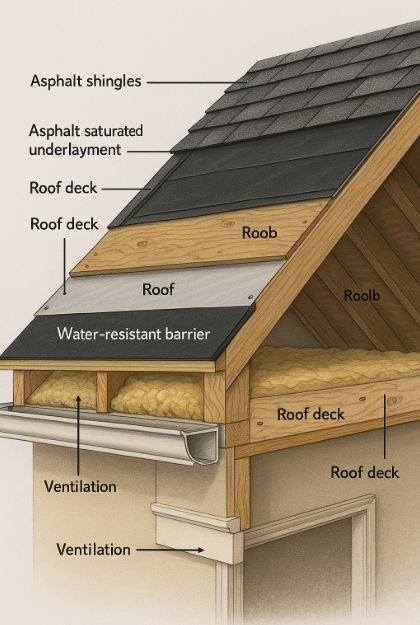
[Image: Cross-sectional diagram showing layers and components of a complete roofing system]
Climate-Specific Considerations
The Insurance Institute for Business and Home Safety provides recommendations for regional roofing adaptations:
- High-wind regions – Enhanced fastening systems, specialized shingle designs, and wind warranties
- Hail-prone areas – Impact-resistant materials with appropriate ratings and insurance benefits
- Heavy snow regions – Structural considerations, ice dam prevention, and appropriate pitch
- Wildfire risk zones – Class A fire-rated materials, non-combustible components, and ember resistance
- Hot/sunny climates – Cool roof technologies, reflective materials, and enhanced ventilation
- Coastal environments – Corrosion-resistant fasteners and components with salt exposure resistance
Investment Considerations
The National Association of the Remodeling Industry provides data on roofing investment factors:
- ROI analysis – National average return of 60-70% for roofing replacement
- Insurance premium impacts – Premium reductions of 5-35% for impact-resistant and fortified roof systems
- Energy efficiency benefits – Cooling cost reductions of 15-30% with ENERGY STAR rated cool roof systems
- Warranty considerations – Manufacturer vs. contractor warranties and transferability benefits
- Property value enhancement – Average property value increases of 5-7% with premium roofing upgrades
Critical Quality Warning
The National Roofing Contractors Association reports that approximately 75% of roofing failures stem from improper installation rather than material defects. Proper installation requires specialized knowledge, appropriate equipment, and strict adherence to manufacturer specifications.
Key risk mitigation strategy: Select contractors certified by material manufacturers, verify proper licensing and insurance, and request detailed installation specifications that address local conditions and building code requirements.
Windows, Doors, and Exterior Trim
Windows, doors, and trim elements significantly impact both energy efficiency and architectural character. According to the Fenestration and Glazing Industry Alliance, these components require careful consideration for optimal performance and aesthetic appeal.
Window Selection Criteria
The Department of Energy’s ENERGY STAR program provides comprehensive guidance on window selection factors:
Window Type | Cost Range (Installed) | Energy Performance | Durability Factors | Best Applications |
---|---|---|---|---|
Vinyl Windows | $300-$800 per window | Good insulation, minimal thermal bridging | Low maintenance, sensitive to extreme heat | Rental properties, budget renovations, moderate climates |
Fiberglass Windows | $500-$1,300 per window | Excellent insulation, minimal expansion | Very durable, stable in temperature extremes | Long-term investments, energy-focused renovations |
Wood Windows | $800-$1,800 per window | Good natural insulation properties | Higher maintenance, susceptible to moisture | Historic properties, premium homes, traditional aesthetics |
Wood-Clad Windows | $700-$1,500 per window | Good insulation with better weather resistance | Moderate maintenance, exterior protection | Upscale properties, wood interior with protected exterior |
Aluminum Windows | $400-$1,100 per window | Poor insulation, high thermal conductivity | Very durable, resistant to weathering | Commercial applications, mild climates, modern aesthetics |
Composite Windows | $500-$1,200 per window | Good to excellent insulation properties | Excellent durability, low maintenance | Various applications, good balance of features |
Source: Department of Energy, Fenestration and Glazing Industry Alliance, manufacturer data (2023)
Energy performance features that significantly impact window efficiency include:
- Multiple glazing layers – Double or triple panes providing enhanced insulation
- Low-E coatings – Microscopically thin metal layers that reflect infrared energy
- Gas fills – Argon or krypton between panes to reduce heat transfer
- Insulated frames – Thermal breaks and cavity insulation within frame components
- Warm-edge spacers – Non-metallic spacers reducing thermal bridging at glass edges
- Weather-stripping quality – Multiple contact points reducing air infiltration
Exterior Door Considerations
The Door and Hardware Institute provides data on exterior door selection factors:
- Material options – Key characteristics and applications:
- Fiberglass: Excellent insulation, low maintenance, wood-look options ($700-$2,500 installed)
- Steel: Strong security, moderate insulation, susceptible to denting ($500-$1,800 installed)
- Wood: Classic appearance, higher maintenance needs, customizable ($1,000-$5,000+ installed)
- Aluminum/Glass: Modern aesthetic, typically less energy efficient ($1,000-$3,500 installed)
- Energy efficiency factors – Components affecting door performance:
- Core insulation: Foam-filled cores providing superior thermal resistance
- Weatherstripping: Multiple contact points with compression seals
- Threshold design: Adjustable thresholds with proper sealing
- Glass content: Amount and type of glazing affecting overall efficiency
- Security features – Elements enhancing protection:
- Deadbolt options: Single vs. double cylinder, smart lock integration
- Strike plate reinforcement: Extended plates with longer screws
- Hinge security: Non-removable pins, extra mounting points
- Door construction: Solid cores, reinforced stiles and rails
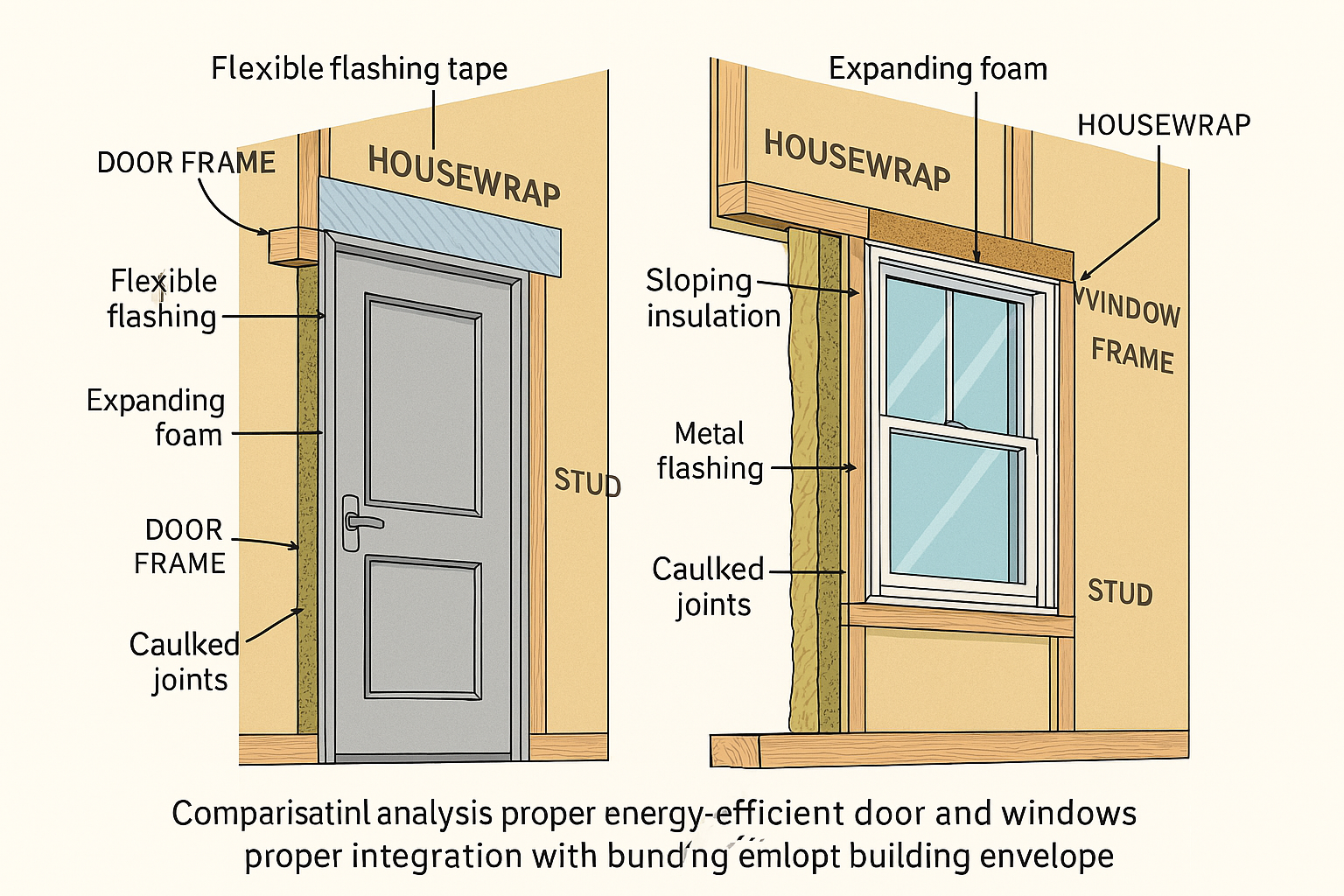
[Image: Detailed installation diagram highlighting proper door and window integration with building envelope]
Exterior Trim Elements
The Architectural Woodwork Institute notes that exterior trim significantly impacts both weather protection and aesthetic appeal:
- Material options – Performance characteristics and applications:
- PVC/Cellular PVC: Zero maintenance, excellent rot resistance, moderate cost ($4-$8 per linear foot)
- Fiber Cement: Durable, paintable, moderate maintenance ($3-$7 per linear foot)
- Wood: Traditional appearance, higher maintenance, various species ($2-$12 per linear foot)
- Engineered Wood: Moderate durability, reduced maintenance ($3-$6 per linear foot)
- Composite: Low maintenance, stable, various formulations ($5-$10 per linear foot)
- Key trim elements – Critical components affecting appearance and protection:
- Fascia boards: Protecting roof edge and supporting gutters
- Soffits: Enclosing eave undersides with proper ventilation
- Window/door casings: Framing openings and providing weather protection
- Corner boards: Finishing exterior corners and protecting sheathing
- Frieze boards: Horizontal trim elements at wall-roof junctions
Research from the National Association of Home Builders indicates that thoughtfully selected and properly installed windows, doors, and trim elements can increase property valuation by 3-5% while enhancing buyer appeal and first impressions. Furthermore, energy-efficient doors and windows can reduce heating and cooling costs by 15-25%, providing ongoing value to owners and tenants.
Decks, Patios, and Outdoor Living Spaces
Outdoor living spaces significantly enhance property functionality and market appeal. According to the National Association of Realtors’ “Remodeling Impact Report,” outdoor improvements consistently rank among the highest-ROI exterior investments.
Deck and Porch Materials
The North American Deck and Railing Association provides comparative data on decking materials:
Decking Material | Cost Range (Installed) | Expected Lifespan | Maintenance Requirements | Key Considerations |
---|---|---|---|---|
Pressure-Treated Wood | $15-$25 per sq ft | 15-20 years | High (annual cleaning, staining every 2-3 years) | Budget-friendly, prone to warping, requires regular care |
Cedar/Redwood | $25-$40 per sq ft | 20-30 years | Moderate-High (cleaning, sealing every 2-3 years) | Natural beauty, resistant to insects, weathering leads to silver-gray patina |
Composite Decking | $30-$60 per sq ft | 25-30 years | Low (occasional cleaning) | No splintering, no staining, wide color options, higher initial cost |
PVC Decking | $35-$65 per sq ft | 25-30+ years | Very Low (occasional cleaning) | Completely synthetic, no organic content, resists staining, highest initial cost |
Tropical Hardwood | $40-$75 per sq ft | 30-50 years | Moderate (annual cleaning, occasional oiling) | Extremely dense, naturally rot-resistant, premium appearance |
Aluminum Decking | $45-$70 per sq ft | 40+ years | Very Low (occasional cleaning) | Non-combustible, won’t rot/warp/crack, specialized applications |
Source: North American Deck and Railing Association, Home Innovation Research Labs (2023)
Patio and Hardscape Options
The Interlocking Concrete Pavement Institute provides data on various hardscape options:
- Concrete patios – Options and characteristics:
- Poured concrete: $8-$15 per sq ft, versatile, moderate lifespan with proper installation
- Stamped concrete: $15-$25 per sq ft, decorative patterns mimicking stone or pavers
- Stained/colored concrete: $10-$20 per sq ft, enhanced aesthetic appeal through coloration
- Pavers and stone options – Materials and applications:
- Concrete pavers: $15-$25 per sq ft, wide design variety, good durability
- Clay brick pavers: $18-$30 per sq ft, classic appearance, long-lasting color
- Natural stone: $25-$50+ per sq ft, premium appearance, excellent durability
- Porcelain tile: $20-$35 per sq ft, low maintenance, modern aesthetic
- Installation considerations – Factors affecting performance:
- Base preparation: Proper compacted aggregate base critical for longevity
- Drainage planning: Slope and permeability considerations to manage water
- Edge restraints: Necessary to maintain stability and prevent spreading
- Jointing materials: Sand, polymeric sand, or mortar options based on application
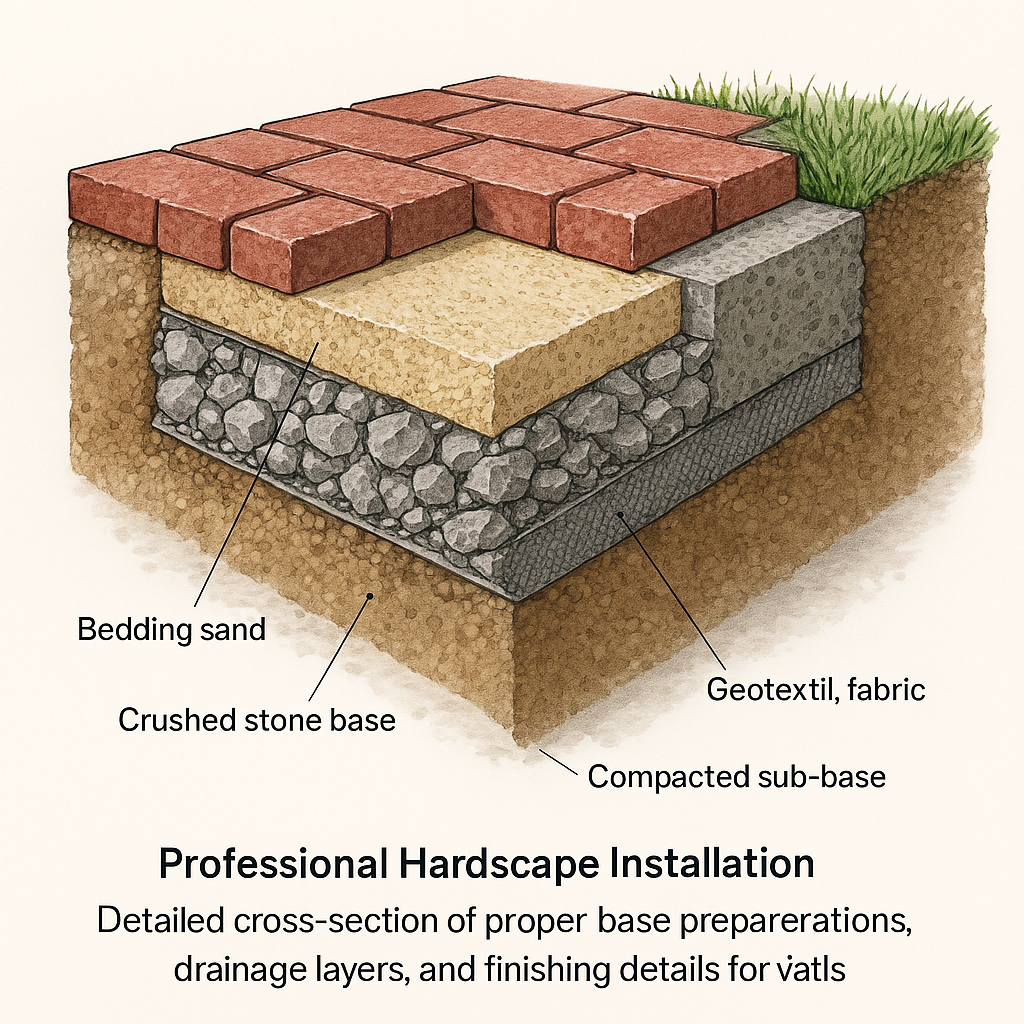
[Image: Detailed cross-section of proper hardscape installation techniques for different materials]
Return on Investment Factors
Remodeling Magazine’s Cost vs. Value Report provides ROI data on outdoor living improvements:
- Wood deck addition – National average ROI of 65-75%, higher in warmer climates
- Composite deck addition – National average ROI of 60-70%, higher in premium markets
- Patio installation – National average ROI of 55-65%, varies by material and design
- Outdoor kitchen – ROI of 50-70% for well-designed spaces in appropriate climates
- Covered porch addition – ROI of 65-90% depending on design and climate
The National Association of Realtors reports that 85% of buyers consider outdoor living space “important” or “very important” in their purchasing decisions, with properly designed and executed spaces potentially reducing time-on-market by 20-30%.
Investment Perspective: Outdoor Space Optimization
According to the American Society of Landscape Architects, strategic outdoor improvements that maximize ROI include:
- Scale-appropriate designs: Outdoor spaces proportional to property size and value (typically 10-15% of property value)
- Function-first planning: Prioritizing usability over elaborate features to maximize practical value
- Climate-responsive elements: Adding features that extend seasonal use such as covered areas, outdoor heating, or shade structures
- Low-maintenance materials: Selecting durable, easy-care materials that reduce ongoing costs
- Strategic lighting: Installing quality outdoor lighting that enhances safety and extends usability into evening hours
Builds and Buys Approach: Exterior Finishes Framework
At Builds and Buys, we’ve developed a systematic approach to exterior finish selection and implementation that maximizes investment returns while ensuring proper system performance:
Step-by-Step Builds: Exterior Implementation Strategy
Our comprehensive approach to new construction and renovation projects:
- Climate-specific material selection – Tailoring exterior systems to local weather patterns and challenges
- Layered protection design – Creating integrated weather barriers with proper flashing and moisture management
- Energy performance integration – Balancing aesthetic considerations with thermal efficiency
- Contractor qualification protocol – Selecting installation professionals with proven expertise
- Quality verification standards – Implementing inspection processes at critical installation phases
Step-by-Step Buys: Exterior Evaluation Framework
For investors evaluating existing properties, our assessment framework provides critical insights:
- Exterior condition assessment – Evaluating current state and remaining useful life of major components
- Weather vulnerability analysis – Identifying potential weak points in the building envelope
- Energy efficiency evaluation – Assessing thermal performance and upgrade opportunities
- Curb appeal enhancement planning – Developing prioritized improvement strategies
- Maintenance requirement projection – Forecasting ongoing care needs based on materials and conditions
Step-by-Step Invest: Financial Optimization
Our investment strategies help allocate exterior improvement budgets for maximum financial performance:
- ROI-driven material selection – Identifying exterior finishes with optimal return on investment
- Visual impact prioritization – Creating perceived value through strategic exterior enhancements
- Insurance cost analysis – Selecting materials that minimize premiums and maximize protection
- Lifecycle cost projection – Balancing initial costs with long-term maintenance requirements
- Incentive opportunity identification – Leveraging available rebates, tax credits, and utility programs
Quality Assurance and Maintenance Protocols
Implementing systematic quality verification and maintenance procedures ensures that exterior finishes deliver their intended performance and longevity. The following inspection protocols are derived from recommendations by the National Association of Home Builders and industry trade organizations.
Siding and Weather Barrier Inspection
- ☐ Weather-Resistant Barrier
- ☐ Proper housewrap/building paper installation
- ☐ Appropriate overlaps and seam treatments
- ☐ Proper integration with flashing components
- ☐ Penetrations properly sealed
- ☐ Drainage planes maintained where required
- ☐ Siding Installation
- ☐ Appropriate fasteners used per manufacturer specifications
- ☐ Proper spacing for expansion/contraction
- ☐ Correct starter strips and accessories
- ☐ Panels/boards level and properly aligned
- ☐ Corner treatments properly executed
- ☐ Moisture Management
- ☐ Appropriate flashing at horizontal transitions
- ☐ Kickout flashing at roof/wall intersections
- ☐ Proper clearances from grade and hardscapes
- ☐ Window and door flashings correctly integrated
- ☐ Drip edges and water diversion details installed
Roofing System Verification
- ☐ Underlayment and Ice Protection
- ☐ Proper underlayment type and installation
- ☐ Ice and water shield at eaves, valleys, and penetrations
- ☐ Proper overlaps and sealing
- ☐ Adequate attachment to substrate
- ☐ Underlayment extended properly at edges
- ☐ Roofing Material Installation
- ☐ Proper nailing pattern and technique
- ☐ Correct exposure and alignment
- ☐ Valley treatments properly executed
- ☐ Adequate offset on successive courses
- ☐ Proper installation at ridges and hips
- ☐ Flashing Details
- ☐ Step flashing at wall intersections
- ☐ Proper counterflashing installation
- ☐ Correct pipe and vent penetration flashing
- ☐ Chimney flashing properly executed
- ☐ Kickout flashing at roof terminations
Window and Door Installation Verification
- ☐ Rough Opening Preparation
- ☐ Opening properly sized per manufacturer requirements
- ☐ Sill pan flashing installed
- ☐ Jamb flashing properly integrated with WRB
- ☐ Head flashing with proper drainage provisions
- ☐ Air barrier continuity maintained
- ☐ Unit Installation
- ☐ Window/door level, plumb, and square
- ☐ Proper shimming with non-deforming materials
- ☐ Fasteners placed per manufacturer requirements
- ☐ Appropriate expansion gap maintained
- ☐ Operational check for proper function
- ☐ Weatherproofing Completion
- ☐ Interior air sealing completed
- ☐ Exterior caulking/sealant application
- ☐ Drip cap flashing properly installed
- ☐ Casing and trim properly integrated
- ☐ Water test performed for verification
Deck and Outdoor Living Inspection
- ☐ Structural Elements
- ☐ Proper footing design and installation
- ☐ Appropriate post-to-beam connections
- ☐ Joist sizing and spacing per code
- ☐ Proper hardware and fasteners for application
- ☐ Ledger board properly attached and flashed
- ☐ Decking Installation
- ☐ Appropriate fastening method for material
- ☐ Proper spacing between boards
- ☐ End joint staggering pattern
- ☐ Perimeter finish details
- ☐ Surface clean and ready for use/finishing
- ☐ Railing Systems
- ☐ Meets height and structural requirements
- ☐ Properly attached to deck structure
- ☐ Appropriate baluster spacing
- ☐ Graspable handrail where required
- ☐ Hardware appropriate for material combination
Maintenance Protocols by Material
The International Association of Certified Home Inspectors recommends specific maintenance schedules to maximize exterior finish longevity:
- Siding maintenance – Material-specific requirements:
- Vinyl: Annual cleaning, inspect for damage, maintain proper clearances
- Fiber cement: Repaint every 7-15 years, inspect caulking annually, clean as needed
- Wood: Repaint/stain every 3-7 years, inspect annually for damage, maintain 6″ ground clearance
- Metal: Inspect fasteners annually, touch up scratches, clean as needed
- Roofing care – System-specific protocols:
- Asphalt shingles: Annual inspection, clear debris, check for loose/damaged shingles
- Metal roofing: Inspect fasteners annually, remove debris, check for galvanic corrosion
- Tile roofing: Annual inspection for cracked/slipped tiles, clean valleys and gutters
- Wood shakes: Regular cleaning, moss treatment, replacement of damaged shakes
- Window and door maintenance – Preserving performance:
- Operation check: Verify smooth function, adjust hardware as needed
- Weather-stripping: Inspect and replace as needed (typically every 5-10 years)
- Exterior caulking: Inspect annually, replace deteriorated sealant
- Finish maintenance: Refinish wood components per manufacturer schedule
- Outdoor living space care – Preserving function and appearance:
- Wood decking: Clean and refinish every 2-3 years, inspect for damage annually
- Composite decking: Semi-annual cleaning, stain treatment as needed
- Concrete/masonry: Seal according to product specifications, repair cracks promptly
- Structure inspection: Annual verification of structural integrity and connections
Establishing a systematic maintenance program can extend exterior finish lifecycles by 30-50% according to the National Association of Home Builders, representing significant long-term value for property investors.
Discover more essential real estate investment strategies with our comprehensive guides on Step-by-Step Builds, Step-by-Step Buys, and Step-by-Step Invest.
Your Tools
Access your tools to manage tasks, update your profile, and track your progress.
Collaboration Feed
Engage with others, share ideas, and find inspiration in the Collaboration Feed.