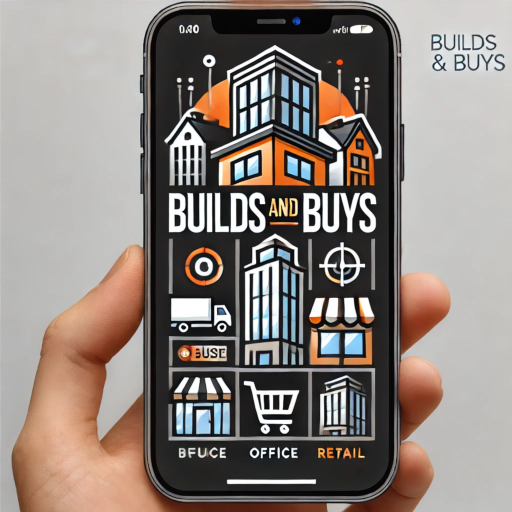
Check out our app!
Explore more features on mobile.
Plumbing and Electrical Systems: Strategic Implementation Guide for Real Estate Investors
Plumbing and electrical systems form the critical infrastructure of any property, directly impacting functionality, safety, compliance, and long-term investment performance. For real estate investors, these systems represent both significant capital expenditures and potential liabilities if improperly designed or installed. Research by the National Association of Home Builders shows that plumbing and electrical issues account for approximately 33% of post-construction warranty claims and can reduce property values by 10-20% when substandard. This comprehensive guide provides real estate investors with essential knowledge to make informed decisions about these crucial building systems.
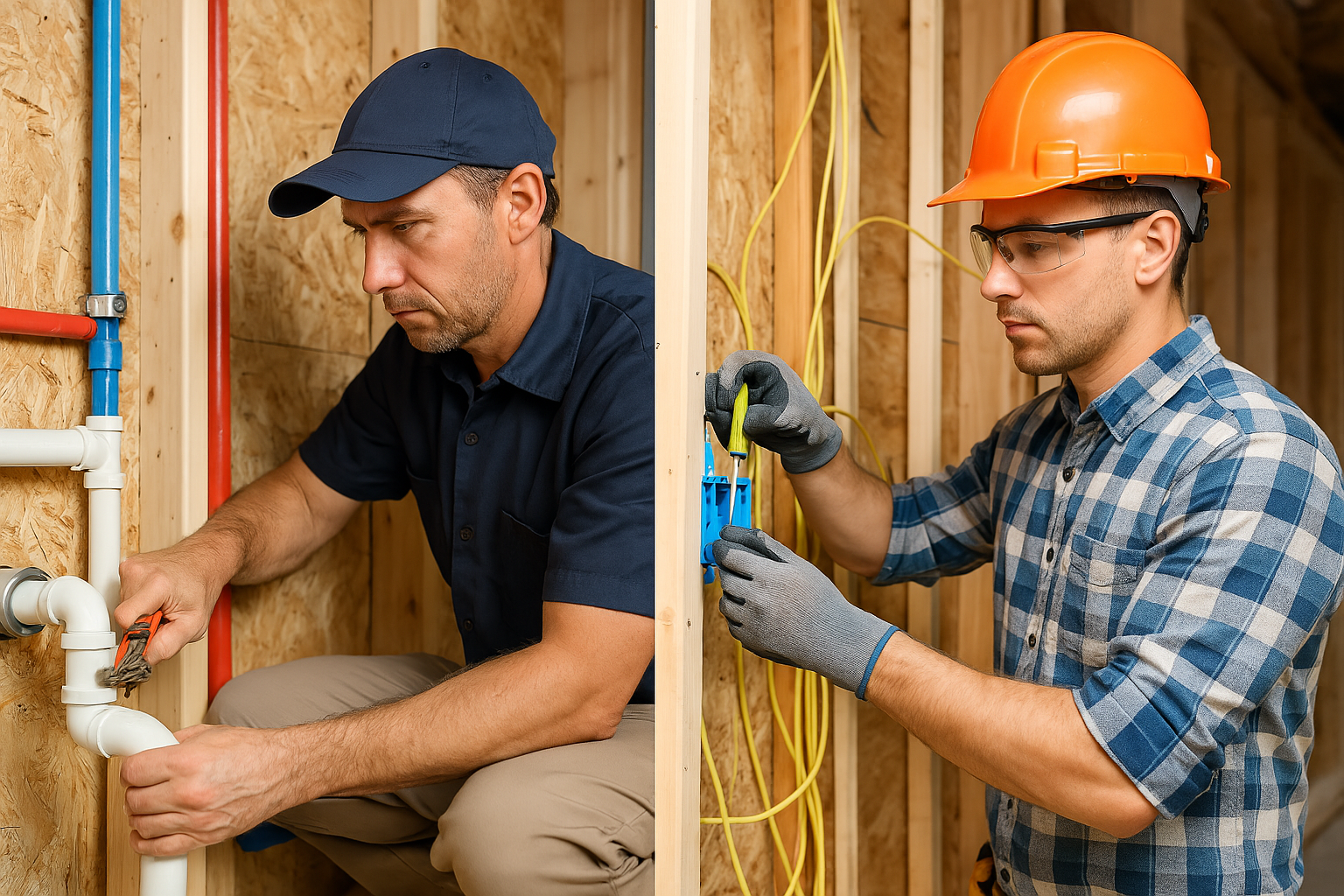
[Image: Professional plumbing and electrical installation with key components labeled]
Strategic Planning for Plumbing and Electrical Systems
Effective planning for plumbing and electrical systems goes beyond meeting basic code requirements to create infrastructure that enhances property value, reduces maintenance costs, and supports future adaptability. According to the Building Owners and Managers Association (BOMA), properly designed systems can reduce operational costs by 15-25% over a 10-year period while minimizing disruptive maintenance issues.
Key strategic considerations include:
- Design for projected usage patterns – Accounting for actual occupancy requirements rather than minimum standards
- Future-proofing considerations – Incorporating capacity for evolving technological and lifestyle needs
- Accessibility planning – Ensuring systems can be serviced without extensive demolition
- Energy and water efficiency – Balancing upfront costs with long-term operational savings
- Material quality decisions – Evaluating lifecycle costs versus initial savings
System Integration Planning
Coordination between plumbing, electrical, HVAC, and structural systems represents a critical success factor often overlooked by investors. Research by the Construction Industry Institute indicates that proper systems integration can:
- Reduce construction conflicts by up to 65%
- Minimize costly field changes and rework
- Decrease overall project timelines by 8-12%
- Optimize spatial requirements and reduce wasted space
- Improve overall system performance and efficiency
A structured approach to system integration includes:
- 3D coordination meetings – Systematic review of all building systems in relation to each other
- Clash detection protocols – Identifying and resolving conflicts before construction begins
- Service pathway planning – Designating clear routes for utilities with adequate clearances
- Load calculation coordination – Ensuring electrical systems support mechanical equipment needs
- Construction sequencing strategy – Defining logical installation sequences to minimize conflicts
Plumbing System Components and Design Considerations
Plumbing systems consist of several interconnected components that work together to provide water supply, waste removal, and gas distribution when applicable. According to the Plumbing-Heating-Cooling Contractors Association, plumbing typically represents 10-15% of total construction costs, with significant variations based on property type, fixture count, and material selections.
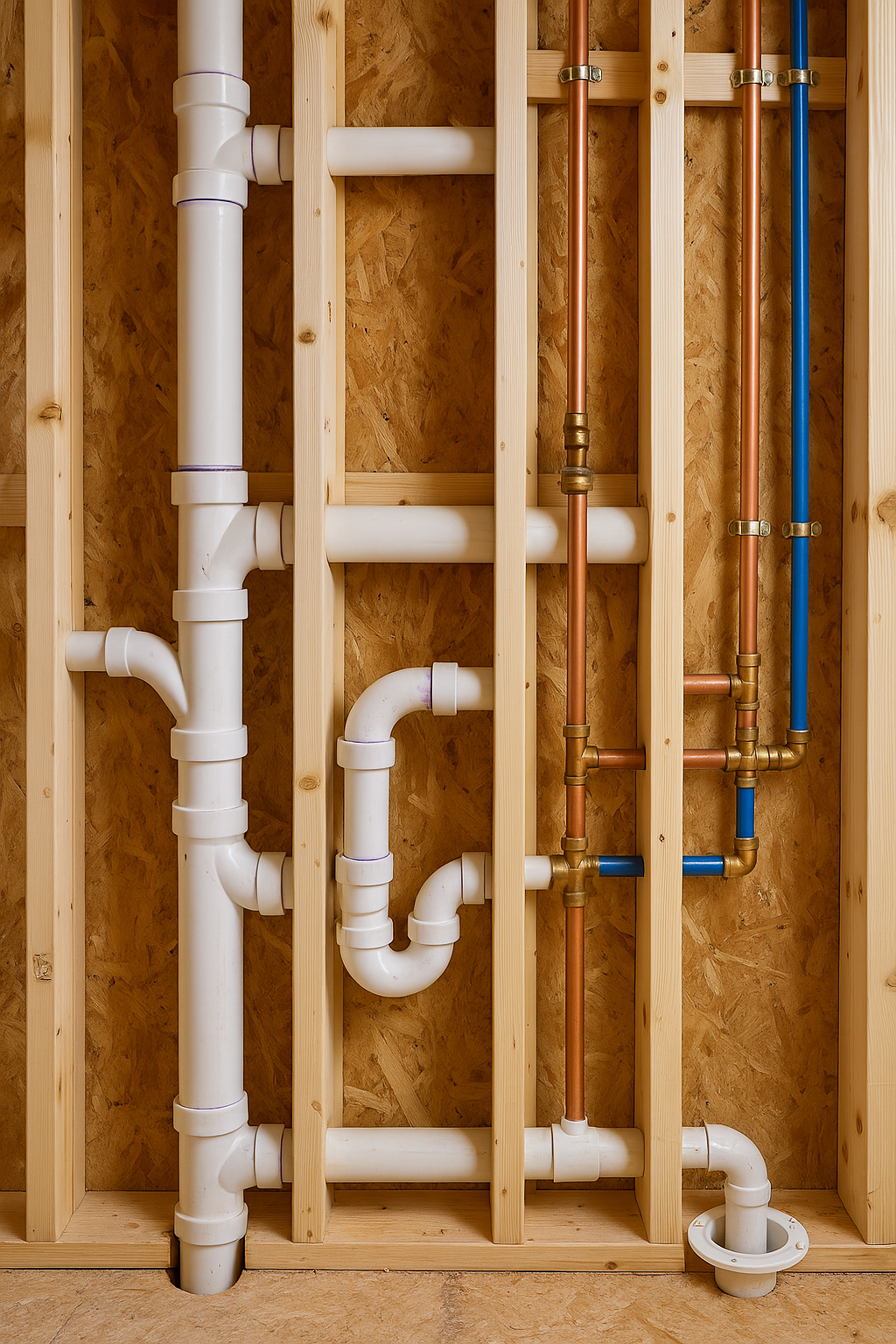
Water Supply Systems
The water supply system delivers clean, potable water throughout the property under appropriate pressure. Key components and considerations include:
- Pipe material selection – Options include copper, CPVC, PEX, and stainless steel, each with distinct advantages:
- Copper: Durable (50+ year lifespan), bacteria-resistant, higher material and labor costs
- PEX: Flexible, freeze-resistant, 25-40 year lifespan, typically 30-40% lower installation cost than copper
- CPVC: Moderate cost, good chemical resistance, moderate difficulty installation
- Stainless Steel: Premium durability, corrosion resistance, highest material cost
- Main supply sizing – Engineering calculations based on fixture count and simultaneous demand
- Pressure regulation – Ensuring consistent 40-80 psi throughout the system
- Isolation valves – Strategic placement for serviceability of specific zones or fixtures
- Insulation requirements – Preventing energy loss and condensation issues
Drain-Waste-Vent (DWV) Systems
The DWV system safely removes wastewater while preventing sewer gases from entering the building. The National Association of Home Builders identifies improper DWV design as a leading cause of costly post-construction plumbing issues. Key considerations include:
- Pipe material options – Typically PVC, cast iron, or ABS with these considerations:
- PVC: Cost-effective, lightweight, chemical resistant, moderate sound transmission
- Cast Iron: Superior sound dampening, longer lifespan, significantly higher material and labor costs
- ABS: Similar to PVC but with better impact resistance in cold temperatures
- Slope requirements – Maintaining proper gradient (typically 1/4″ per foot for branches, 1/8″ per foot for mains)
- Venting design – Ensuring adequate air flow to prevent trap siphoning
- Cleanout placement – Strategic locations for maintenance access
- Noise mitigation strategies – Especially important in multi-family or premium properties
Fixture Selection and Placement
Plumbing fixtures represent the visible, functional elements of the system and significantly impact both user experience and property value. According to Remodeling Magazine’s Cost vs. Value Report, bathroom and kitchen upgrades consistently provide some of the highest returns on investment for property improvements. Considerations include:
- Water efficiency standards – WaterSense certification reduces consumption by 20% or more
- Fixture quality tiers – Builder-grade vs. premium options with associated cost implications
- Universal design features – Accessibility considerations for maximum market appeal
- Style longevity – Balancing trends with timeless designs for long-term value
- Material and finish durability – Impact on maintenance requirements and replacement frequency
Fixture Category | Economy Grade Cost Range | Premium Grade Cost Range | Key Investment Considerations |
---|---|---|---|
Toilets | $150-300 | $400-800+ | Water efficiency, flushing performance, bowl shape, height |
Bathroom Faucets | $50-150 | $200-600+ | Finish durability, cartridge quality, water efficiency |
Shower Systems | $200-500 | $800-3,000+ | Valve quality, pressure balance features, spray options |
Kitchen Faucets | $100-250 | $300-1,000+ | Functionality, spray features, finish durability |
Water Heaters | $400-800 | $1,200-3,000+ | Tank vs. tankless, energy efficiency, recovery rate |
Water Heating Systems
Water heating typically represents 14-18% of residential energy use according to the Department of Energy. System selection involves balancing upfront costs with operational efficiency:
- System types – Options include:
- Conventional tank: Lower initial cost, higher operating expenses, 10-15 year lifespan
- Tankless on-demand: 40-60% higher initial cost, 25-35% energy savings, 20+ year lifespan
- Heat pump water heaters: High efficiency, moderate installation complexity, best in moderate climates
- Point-of-use systems: For remote fixtures or supplemental capacity
- Sizing considerations – Based on occupancy, fixture count, and simultaneous demand
- Fuel type options – Natural gas, propane, electric, and solar with varying operational costs
- Location planning – Minimizing pipe runs to reduce heat loss and wait times
- Recirculation systems – Balancing convenience with energy consumption
Electrical System Planning and Implementation
Electrical systems represent approximately 7-10% of total construction costs according to RSMeans construction data, yet they significantly impact safety, functionality, and future adaptability of properties. According to the Electrical Safety Foundation International, electrical system failures contribute to over 51,000 residential fires annually, underscoring the importance of proper design and installation.
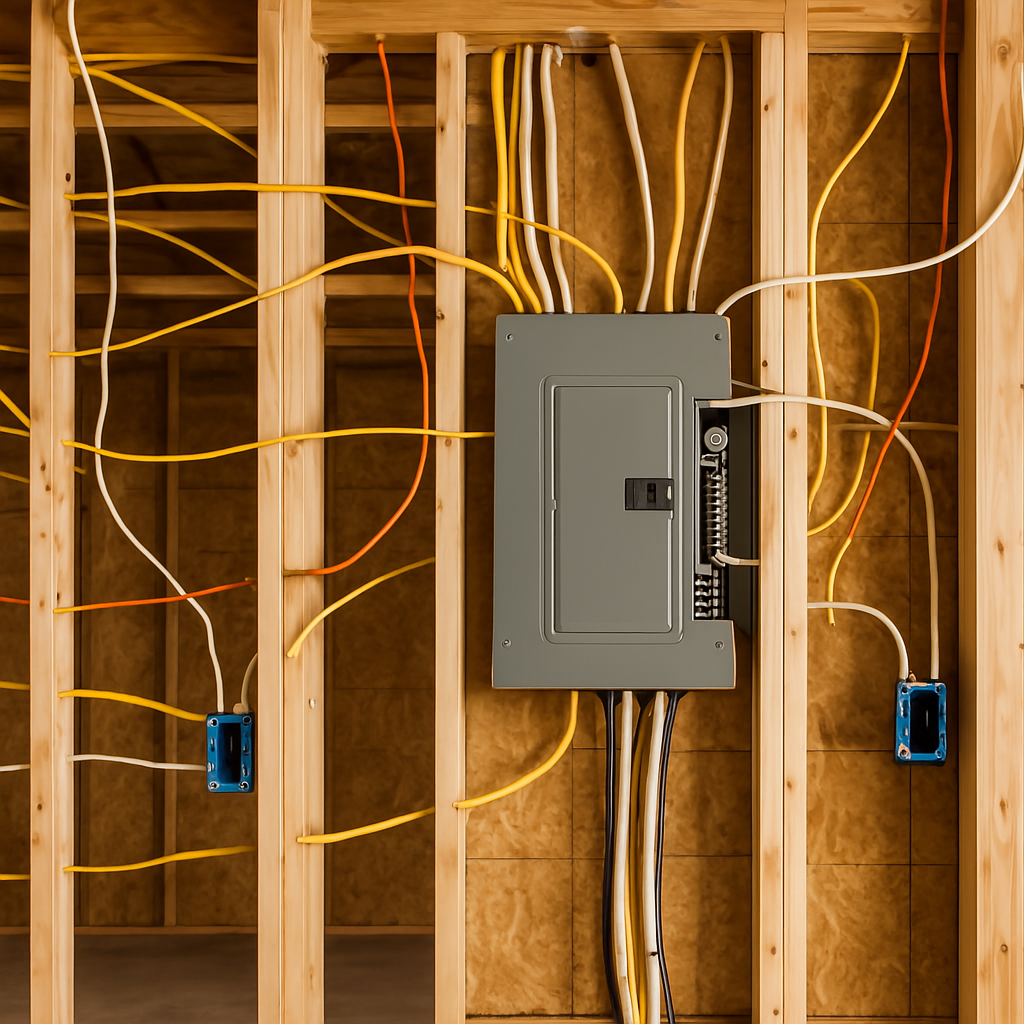
Service Size and Panel Considerations
The electrical service represents the total capacity available to the property. The National Electrical Contractors Association recommends considering both current and future needs when sizing electrical services:
- Service capacity options – Common residential services include:
- 100 Amp: Minimum for small residences, increasingly inadequate for modern demands
- 150 Amp: Standard for moderate-sized homes with basic electrical appliances
- 200 Amp: Currently standard for new construction, accommodates most modern needs
- 320/400 Amp: For larger homes or properties with extensive electrical demands
- Panel quality tiers – Variations in reliability, safety features, and expansion capacity
- Subpanel planning – Strategic use for remote areas or specific loads
- Location considerations – Accessibility, code compliance, and protection from damage
- Surge protection integration – Whole-house systems to protect sensitive electronics
Circuit Design and Distribution
Proper circuit planning ensures safety, prevents nuisance tripping, and supports operational needs. The Electrical Safety Foundation International identifies inadequate circuit distribution as a leading cause of electrical fires:
- Dedicated circuit requirements – For major appliances and specific applications
- Circuit segregation strategy – Separating lighting from receptacle circuits
- AFCI/GFCI protection – Locations and types required by current codes
- Load calculation methodology – Determining appropriate circuit capacity for various uses
- Voltage considerations – 120V vs 240V applications and appropriate wiring
Circuit Type | Typical Amperage | Recommended Applications | Special Requirements |
---|---|---|---|
General Lighting | 15A | Room lighting, ceiling fans, light-duty receptacles | AFCI protection in most living spaces |
General Receptacles | 15A or 20A | Wall outlets for general use | AFCI protection, maximum 8-10 outlets per circuit |
Kitchen Receptacles | 20A | Counter-top small appliances | GFCI protection, minimum two dedicated circuits |
Major Appliances | 20A-50A | Refrigerator, dishwasher, disposal, microwave | Dedicated circuit for each appliance |
HVAC Equipment | 30A-60A | Air conditioning, heat pumps, electric furnaces | Disconnect within sight, sized to equipment |
Bathroom Circuits | 20A | Outlets for hair dryers, electric shavers, etc. | GFCI protection required for all outlets |
Wiring Methods and Materials
Wiring selection impacts safety, longevity, and future flexibility of electrical systems:
- Conductor material options – Considerations include:
- Copper: Superior conductivity, longevity, higher material cost
- Aluminum: Lower cost, higher expansion rates, specific connection requirements
- Copper-clad aluminum: Compromise option with moderate performance
- Wire insulation types – THHN, XHHW, NM-B (Romex), UF-B with varying applications
- Conduit vs. cable systems – Flexibility, protection, and future adaptability considerations
- Homerun planning – Efficient routing to minimize materials and voltage drop
- Future access considerations – Planning for modification and expansion capability
Lighting Design and Controls
According to the Department of Energy, lighting accounts for approximately 15% of residential electricity use. Strategic lighting design affects both energy consumption and property marketability:
- Fixture selection considerations – Balancing aesthetics with efficiency and longevity
- LED integration strategy – Leveraging 75-80% energy savings over incandescent options
- Control system options – Simple switches, dimmers, occupancy sensors, or smart controls
- Color temperature planning – Appropriate Kelvin ranges for different spaces and uses
- Layered lighting approach – Ambient, task, and accent lighting for functional elegance
Smart Home and Technology Integration
The Consumer Technology Association reports that 69% of homebuyers are willing to pay premiums for homes with smart technology features. Planning for technology infrastructure involves:
- Structured wiring systems – Future-ready pathways for communication and data
- Wireless system support – Planning for optimal Wi-Fi coverage throughout the property
- Smart device integration – Infrastructure for connected thermostats, lighting, security, etc.
- Charging station considerations – USB outlets and dedicated charging areas
- Future-proofing strategies – Conduit pathways and access points for evolving technology
Code Compliance and Permitting Requirements
Plumbing and electrical systems are heavily regulated due to their impact on public health, safety, and welfare. According to the International Association of Plumbing and Mechanical Officials, non-compliant installations represent significant liability for property owners and investors. Understanding the regulatory landscape is essential for risk management and project success.
Building Code Framework
The regulatory structure for plumbing and electrical systems includes multiple layers:
- Model codes – Developed by national organizations such as:
- International Plumbing Code (IPC) or Uniform Plumbing Code (UPC)
- National Electrical Code (NEC/NFPA 70)
- International Residential Code (IRC) with plumbing and electrical provisions
- State adoption and amendments – Modifications to model codes at the state level
- Local jurisdiction requirements – Additional city or county-specific provisions
- Code cycle awareness – Understanding which edition is currently enforced
- Retroactive requirements – When upgrades to existing systems become mandatory
Permitting Process Overview
The National Association of Home Builders reports that permitting and inspection processes add approximately 2-5% to project costs but provide essential quality assurance and liability protection. Key elements include:
- Plan review requirements – Documentation needed for permit application
- Permit fee structures – Typically based on project valuation or specific fee schedules
- Inspection sequencing – Critical verification points during installation
- Common correction items – Frequent code compliance issues to avoid
- Documentation management – Maintaining records of permits, inspections, and approvals
Licensing and Qualification Requirements
Most jurisdictions restrict plumbing and electrical work to qualified professionals:
- Contractor licensing categories – Varying levels based on complexity and risk
- Journeyman and master certifications – Individual qualification requirements
- Insurance and bonding requirements – Financial protection mandates
- Continuing education obligations – Ongoing training to maintain qualifications
- Owner-builder provisions – When property owners can perform their own work
Common Compliance Challenges
The International Code Council identifies several recurring compliance issues that impact both safety and project timelines:
- Minimum clearance violations – Inadequate working space around equipment and panels
- Support and anchoring deficiencies – Improper securing of pipes, conduits, and fixtures
- Mixed material concerns – Improper transitions between different piping or wiring types
- Protection requirements – Inadequate shielding from physical damage or environmental factors
- Testing and verification failures – Pressure testing, ground fault detection, and other verification issues
Critical Compliance Warning
The Consumer Product Safety Commission reports that code violations in electrical systems contribute to over 50,000 residential fires annually, while plumbing system failures cause billions in water damage. Beyond the immediate safety concerns, non-compliant work discovered during resale inspections can significantly impact property values and transaction timelines.
Key risk mitigation strategies: Hire licensed professionals, obtain proper permits, maintain documentation of inspections and approvals, and require contractors to warranty their work for both performance and code compliance.
Cost Analysis and Investment Considerations
Understanding the comprehensive cost structure of plumbing and electrical systems helps investors make informed decisions that balance initial expenditures with long-term performance. According to construction cost data from RSMeans, these systems typically represent 15-25% of total construction costs for residential properties.
System Component | Economy Tier Cost Range | Premium Tier Cost Range | Key Value Considerations |
---|---|---|---|
Plumbing Rough-In | $4.50-6.00/sq ft | $7.00-10.00/sq ft | Pipe material quality, future accessibility, water efficiency |
Plumbing Fixtures | $2,500-4,500 per bath | $5,000-15,000+ per bath | Material quality, warranty periods, water efficiency, style longevity |
Water Heating System | $1,000-1,800 installed | $3,000-7,000+ installed | Energy efficiency, capacity, recovery rate, lifespan, warranty |
Electrical Service | $1,800-3,000 (100-150A) | $3,500-7,000 (200-400A) | Capacity for future needs, panel quality, safety features |
Electrical Distribution | $3.00-4.50/sq ft | $5.00-9.00/sq ft | Circuit density, outlet quantity, conductor quality |
Lighting Package | $1,200-3,000 | $4,000-15,000+ | Fixture quality, energy efficiency, design impact, controls |
Technology Integration | $500-1,500 | $3,000-10,000+ | Structured wiring, smart home readiness, expansion capacity |
Investment Performance Factors
According to the National Association of Realtors, certain plumbing and electrical investments consistently deliver strong returns when properly aligned with market expectations:
- Market alignment strategy – Matching system quality to neighborhood standards and price points
- Energy efficiency premium – High-efficiency systems command 1-3% higher property values in many markets
- Technological differentiation – Smart home features can reduce time-on-market by 20-30% in competitive situations
- Warranty value proposition – Transferable warranties on major systems enhance marketability
- Documentation package – Comprehensive records of permits, inspections, and specifications add transaction value
Lifecycle Cost Considerations
The Department of Energy and American Water Works Association provide data showing that initial installation represents only 25-40% of lifetime system costs. Key considerations for total ownership costs include:
- Energy consumption patterns – Operating costs for various system types and efficiency levels
- Maintenance requirements – Regular service needs and associated expenses
- Component replacement cycles – Expected lifespans for various system elements
- Water efficiency impacts – Both direct utility savings and reduced wastewater expenses
- Insurance premium effects – Modern systems often qualify for reduced rates
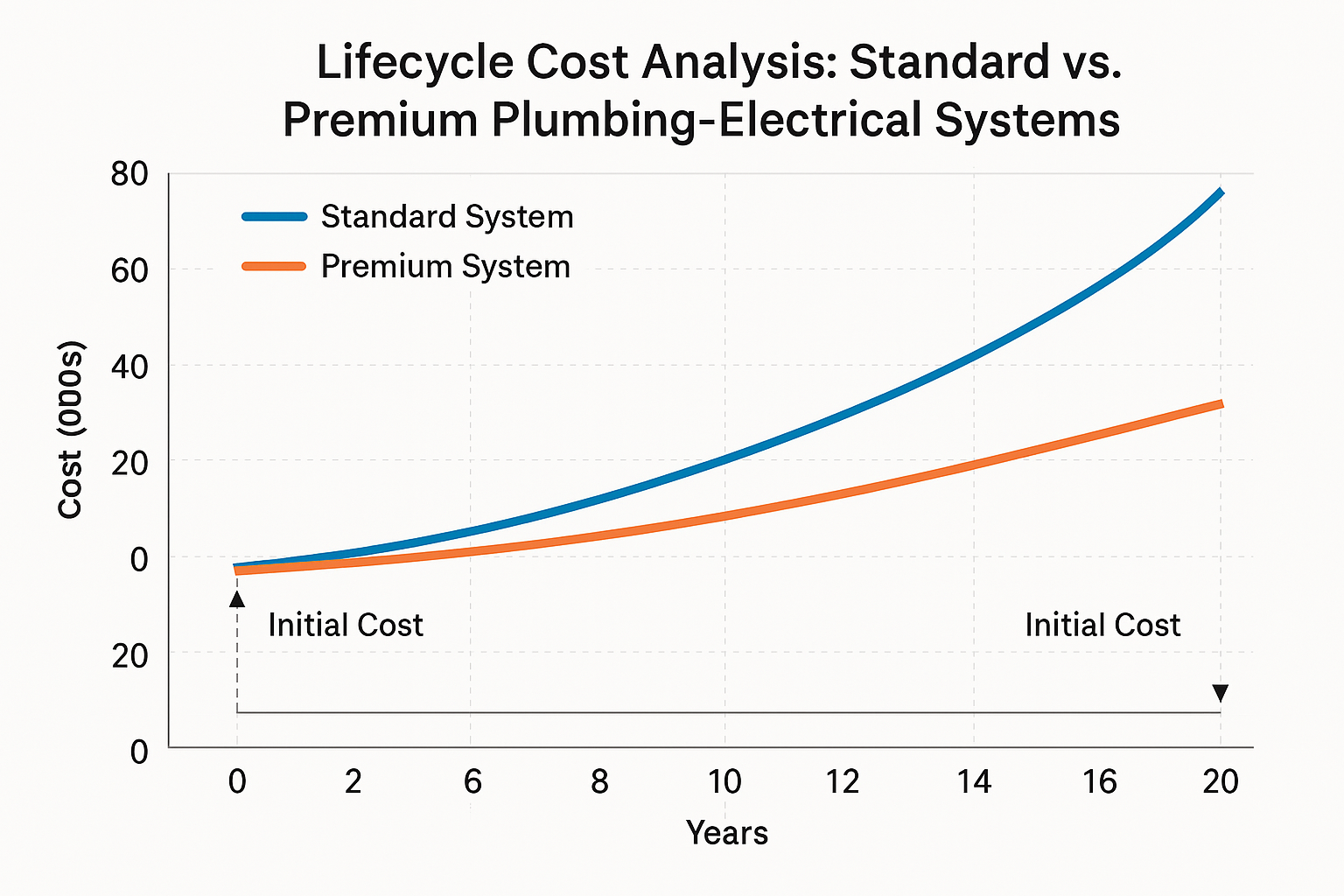
[Image: Comparative lifecycle cost analysis showing initial and operating costs for different system tiers]
Value Engineering Opportunities
The Construction Management Association of America identifies several strategies for optimizing system value without compromising performance:
- Concentration of premium features – Focusing high-end elements in visible, high-impact areas
- Strategic system zoning – Tailoring performance levels to specific property areas
- Alternative material selections – Using newer technologies that offer performance at lower costs
- Design optimization – Minimizing pipe and wire runs through thoughtful layout planning
- Energy efficiency targeting – Identifying investments with the fastest payback periods
Builds and Buys Approach: Plumbing and Electrical Framework
At Builds and Buys, we’ve developed a systematic approach to plumbing and electrical systems that balances initial costs with long-term performance and market value:
Step-by-Step Builds: System Implementation Strategy
Our comprehensive approach to new construction and renovation projects:
- Performance specification development – Creating clear, measurable standards for each system component
- Technology integration planning – Future-proofing designs for evolving needs and capabilities
- Contractor qualification protocol – Selecting specialists with proven expertise and quality history
- Progressive inspection framework – Verification at critical installation points beyond code minimums
- Documentation standards – Creating comprehensive records that enhance property marketability
Step-by-Step Buys: System Assessment Framework
For investors evaluating existing properties, our inspection framework provides critical insights:
- System identification methodology – Recognizing installed components and their implications
- Age and condition evaluation – Assessing remaining useful life and performance capacity
- Deficiency detection protocol – Identifying code violations and safety concerns
- Upgrade opportunity analysis – Evaluating potential improvements and their ROI
- Due diligence documentation – Creating records that support investment decisions
Step-by-Step Invest: System Financial Optimization
Our investment strategies help allocate resources for maximum financial performance:
- Market-specific standards analysis – Determining appropriate quality levels for target demographics
- Component-level ROI calculation – Identifying highest-return system elements
- Efficiency incentive maximization – Leveraging available rebates and tax benefits
- Value engineering application – Optimizing designs for maximum performance per dollar
- Exit strategy alignment – Matching system investments to planned holding periods
Quality Assurance and Inspection Checklist
Thorough inspection and verification protocols ensure plumbing and electrical systems meet both code requirements and performance expectations. The following checklist, developed in consultation with master plumbers, electricians, and home inspectors, covers critical evaluation points:
Plumbing System Inspection Checklist
- ☐ Water Supply System
- ☐ Proper pipe material for application and location
- ☐ Adequate pipe sizing for flow requirements
- ☐ Proper support and protection from damage
- ☐ Insulation where required for freezing or condensation
- ☐ Pressure tested to required PSI without leaks
- ☐ Accessible shutoff valves at fixtures and major branches
- ☐ Drain-Waste-Vent System
- ☐ Proper pipe material and connections
- ☐ Correct slope for drainage lines (1/4″ per foot min. for branches)
- ☐ Venting correctly sized and properly terminated
- ☐ Cleanouts accessible at required locations
- ☐ Proper support and protection
- ☐ Air tested or water tested for leaks
- ☐ Fixture Installation
- ☐ Properly secured and sealed to surfaces
- ☐ Water connections leak-free
- ☐ Drainage connections properly trapped and vented
- ☐ Adequate clearances for usage and maintenance
- ☐ Water flow and pressure appropriate
- ☐ Fixture operation tested and verified
- ☐ Water Heating System
- ☐ Properly sized for demand requirements
- ☐ Temperature and pressure relief valve installed and piped
- ☐ Earthquake strapping where required by code
- ☐ Proper venting for fuel type
- ☐ Pan and drain installed where required
- ☐ Expansion tank installed where required
Electrical System Inspection Checklist
- ☐ Service and Distribution
- ☐ Adequate service size for property demands
- ☐ Panel properly installed and secured
- ☐ Required working clearances maintained
- ☐ Panel directory accurate and complete
- ☐ Proper grounding and bonding system
- ☐ Surge protection provisions
- ☐ Circuit Installation
- ☐ Proper wire sizing for loads and distances
- ☐ AFCI protection where required
- ☐ GFCI protection where required
- ☐ Dedicated circuits for required appliances
- ☐ Proper support and protection of cables/conduits
- ☐ Junction boxes accessible and properly covered
- ☐ Devices and Fixtures
- ☐ Outlets and switches properly installed and secured
- ☐ Required spacing of receptacles maintained
- ☐ Lighting fixtures properly supported and connected
- ☐ Weather-resistant outlets where required
- ☐ Tamper-resistant receptacles where required
- ☐ All outlets, switches and fixtures tested for operation
- ☐ Special Systems
- ☐ Smoke and carbon monoxide detectors properly located
- ☐ Low-voltage systems properly separated from line voltage
- ☐ Outdoor circuits weatherproofed appropriately
- ☐ Bathroom and kitchen electrical requirements met
- ☐ HVAC disconnect requirements satisfied
- ☐ Technology infrastructure properly installed
Documentation Verification
- ☐ Permit applications and approvals
- ☐ Rough-in inspection records
- ☐ Final inspection approvals
- ☐ Contractor licenses and insurance verification
- ☐ Manufacturer warranties for fixtures and equipment
- ☐ Contractor workmanship warranties
- ☐ As-built drawings or system documentation
- ☐ Operations and maintenance manuals for equipment
- ☐ Energy efficiency certifications where applicable
Discover more essential real estate investment strategies with our comprehensive guides on Step-by-Step Builds, Step-by-Step Buys, and Step-by-Step Invest.
Your Tools
Access your tools to manage tasks, update your profile, and track your progress.
Collaboration Feed
Engage with others, share ideas, and find inspiration in the Collaboration Feed.